航空機のエンジン整備・JALエンジニアリング
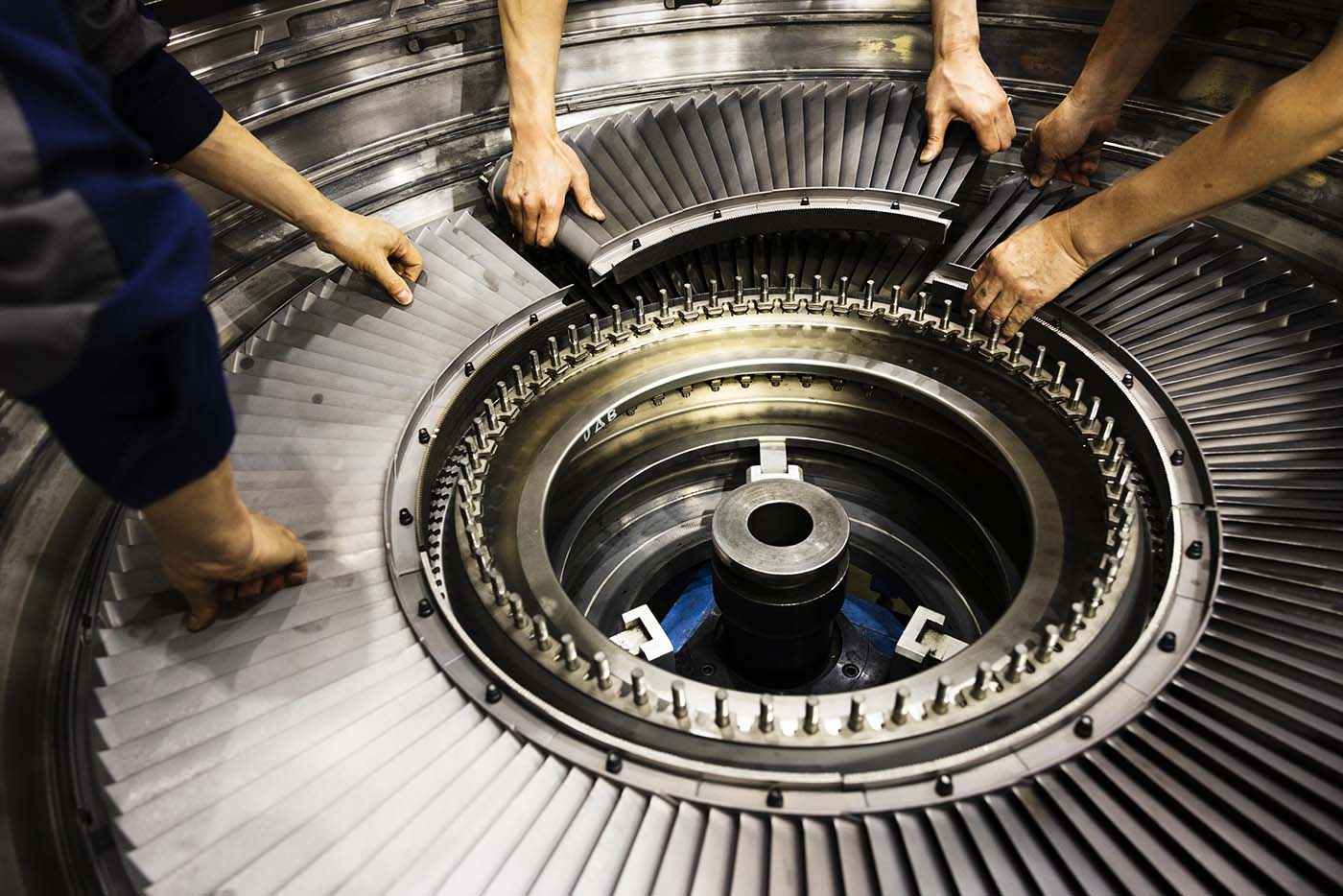
取材協力:株式会社JALエンジニアリング
取材した人:西澤丞
はじめに
3年くらい前、JALエンジニアリングさんにお願いして、格納庫内での整備やランディングギアの整備を取材させてもらったことがある。今回は、その続編ってことでエンジンの整備作業を取材させてもらった。
写真は、2022年に撮ったものと2025年に撮ったものを組み合わせている。インタビューは2025年に行った。

エンジン整備の概要
JALエンジニアリングさんでエンジンの整備に関わっている人は、359人(2025年4月1日現在)。そのうち229人が現場で仕事をしている。整備しているエンジンは、JALさん所有のエンジンと他社さんのエンジンだ。また、JALさんが所有しているエンジンは、全部ここに運び込まれた後、機種によっては他社さんに送って整備をしてもらう。
整備するタイミングは、原則的に「エンジンサイクル」によって管理されている。エンジンは、離陸の時に出力を最大にするので、負担が大きい。また、熱くなったり冷えたりするのもエンジンにとって負担となるので、何回飛んだかという「エンジンサイクル」によって整備のタイミングを判断する。個々のエンジンの状態によって幅があるものの、ボーイング787に搭載されているGEnx-1Bエンジンの場合は、およそ4千サイクルでエンジンを機体から取り外し、定期的な整備をする。なお、整備の回数によって、点検項目が異なってくる。タービンは痛みやすいので、毎回チェックする必要があるが、コンプレッサーは、そこまでではない。ギアボックスのように熱にさらされない部品は、痛みも少ないので3回に一度といった具合だ。
また、定期点検以外のタイミングでも不具合があれば、当然、点検の対象となる。航空機運航中、エンジンのデータは随時モニターされていて、圧力や振動などのパラメータに変化が見られた場合には、適切なタイミングでファイバースコープなどを使って状況を確認し、必要であれば修理などを実施する。なお、各種センサーは、エンジンだけではなく、機体のあらゆるところについていて、一部のデータの解析にはAIも活用されている。

エンジンを整備する工程について
エンジンを整備する工程は、以下の通りだ。今回の取材では、「事前の検査」と「分解」のシーンは撮れなかった。残念。
事前の検査(ファーストインスペクション)
実際に分解する前に、ファイバースコープなどを使ってエンジンの状態を確認する作業。予定ではタービンだけの整備となっていても、この段階で他にも手を入れるべきところがあれば、それも一緒に整備する計画を立てる。
分解
分解する時は、通常のコンディションと違う部分に注意しながら作業する。いつもと色が違う、ボルトの締まり具合が固い、いつもと違うところに傷があるなどの異常があれば、何かしらの原因があるので、それを突き止める必要がある。この辺りは、経験を積まないと分からないことだ。
洗浄
洗浄は、メカニカル洗浄とケミカル洗浄に大別される。メカニカル洗浄にはブラストと呼ばれる作業がある。これは、砂状の粒(酸化アルミニウム)を高圧で吹き付けて表面の汚れを落とす作業だ。ケミカル洗浄は、強酸や強アルカリの液が入ったタンクに部品をつけて化学的に汚れを落とす。部品の素材によっては、洗浄液に弱い物もあるので、分解の段階で部品が混ざらないように、箱の色を分けるなどの工夫をしている。


検査
検査する際の精度は、部品の大きさによっても変わってくる。細かな物では10万分の1インチまで計測し、加工する際の精度も1万分の1の精度が求められる。





修理
修理方法には、溶射、溶接、接着、板金、手仕上げなどがある。溶射とは、高温下で溶けた金属を高圧の圧縮空気で母材に吹き付け、部品の肉厚を回復させたり、表面加工を施す技術だ。また、接着は、カーボンファイバーなどの複合材の使用が増えているため、修理に占める割合が増加している。ただ、温度や圧力、材料の使用期限など、管理しなければいけない要素が多いので大変だとのこと。
また、部品を機械加工する際には、部品の材質や形状によって、温度による寸法の変化があるので、それも考慮に入れなければいけない。どのくらい変動するのかを予測するのは、経験によるものなので、習得するのは大変だ。
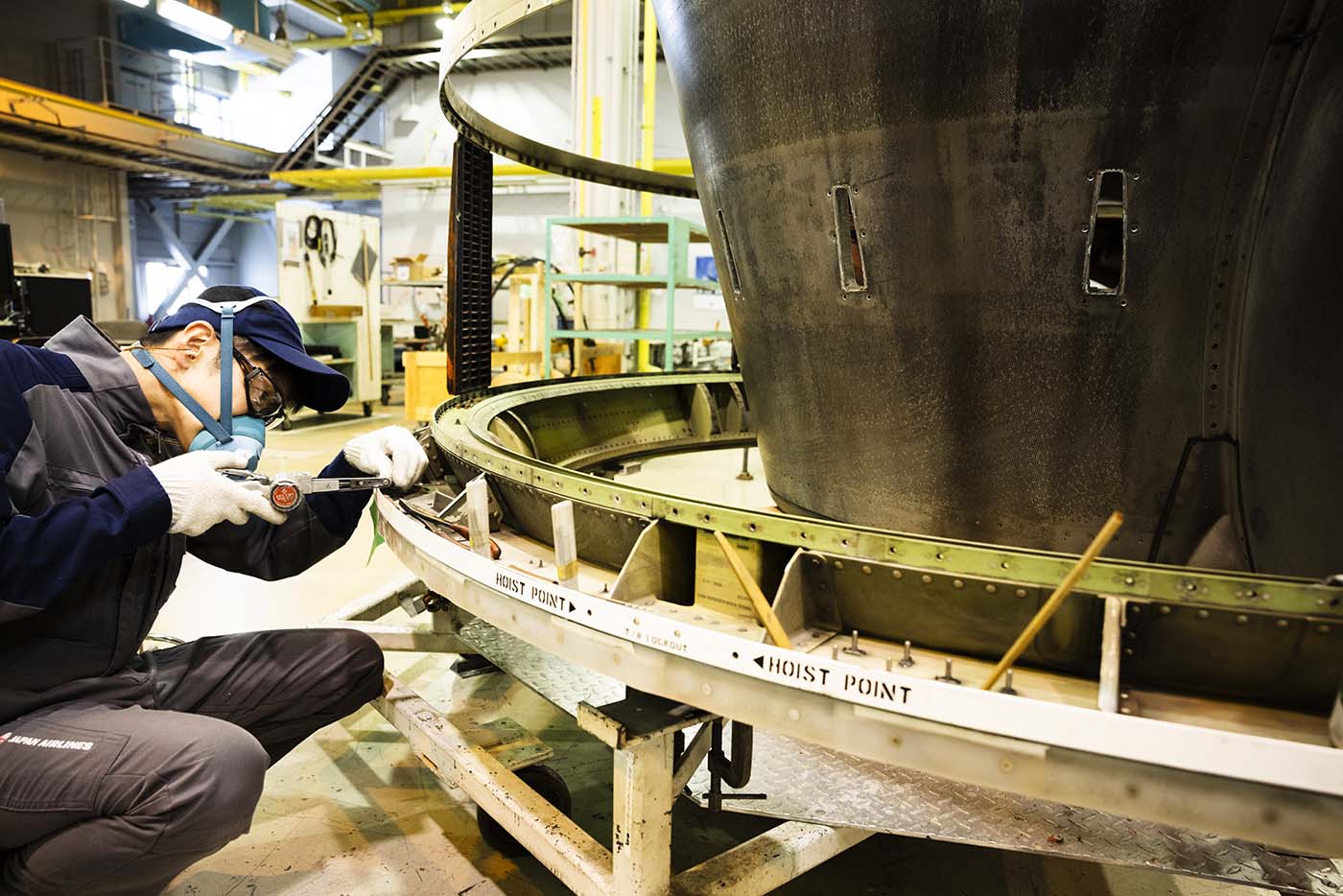
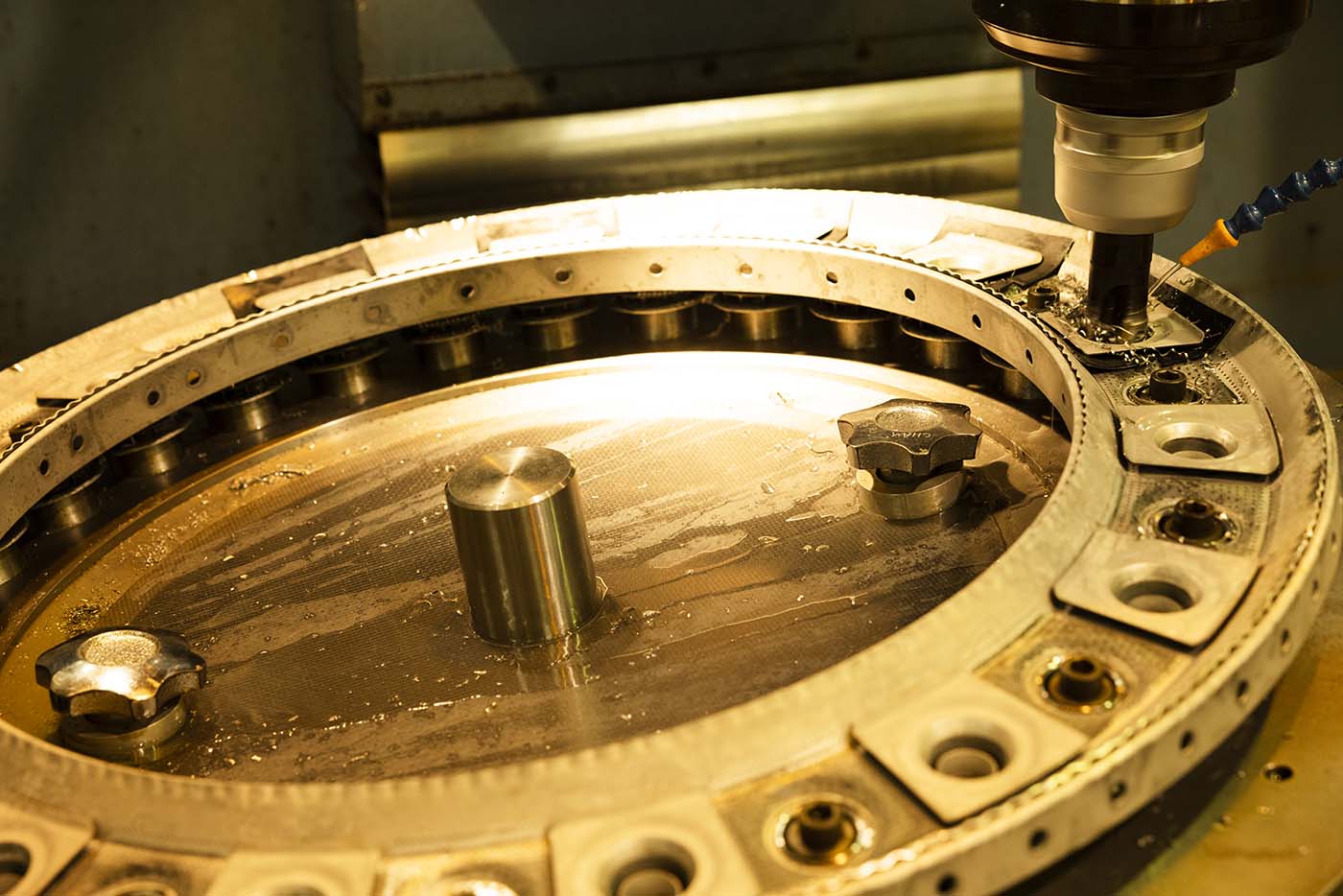
組立
ブレードは高速で回転する物なので、組み立てる時には重量バランスが大切だ。最近では、ブレードの重さや重心位置をコンピューターに入力すると、最適な取り付け位置を教えてくれる。



試運転
試運転は、マニュアルに従って、段階的に実施する。圧縮空気で運転する「モータリング」、低速回転で運転する「アイドル」、高速回転で運転する「ハイパワー」だ。段階に分けて行うのは、安全を確保するためだ。事前に検査をして、不具合がないことを確認してから行うのだが、万が一の事態が起きないための配慮だ。




なお、試験での合否判定はM1資格の整備士が行う。マニュアルに書かれていない事象が現れた場合は、技術部門に相談し、それでも解決しない場合はメーカーに問い合わせることもある。また、整備全般に言えることとして、手で触った時の感触や匂い、色など、人の感覚によって判断しなければいけない要素もかなり多い。
整備士になるには?
JALエンジニアリングさんの場合、高専、航空専門学校、大学のいずれかを卒業した後に採用試験を受ける。採用されてからは、新人教育や整備の基礎訓練を経て、配属部署が決まる。その後は、実務訓練や試験などを通じて、整備士としての資格をレベルアップさせてゆく。過程としては、3ヶ月程度の実務経験で初級整備士M、Mとしての実務経験2年以上でM2、M2としての実務経験3年以上でM1の資格が取れるようになる。なお、この過程については2025年時点での話だ。今までも時代によって変わってきているので、今後の変更もあり得る。
個人的な話を聞いてみた
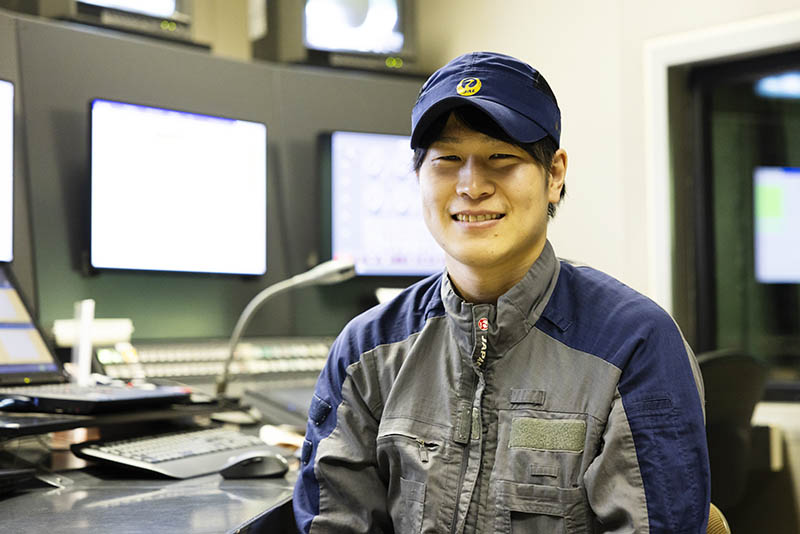
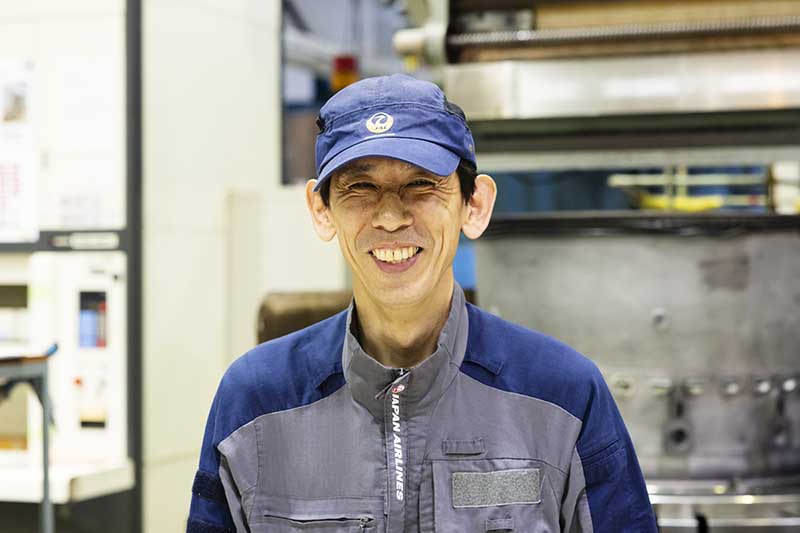
今回、インタビューに答えてくれたのは、若手代表の垣谷悠介さん(28)とベテラン代表の大橋元彦さん(54)だ。垣谷さんは、試運転M1の資格を持つ整備士で、主に試運転の仕事をしつつ、組立や分解を行うこともある。大橋さんは、機械加工M1の資格を持つ修理のスペシャリストだ。
なぜ、航空機の整備士に?
垣谷さん
「整備の業界に興味があって、船舶や電車の整備士も考えたのですが、スキルが高く、お客さまとの距離感が近い整備士はどこかなって考えた時に、航空機かなと思いました。エンジン整備センターに配属されたのは、希望を出したからです。現在、試運転でのM1資格を持っています。」
大橋さん
「単純に航空業界への憧れがありました。配属先に関しては、希望を聞かれることもなく機械加工の職場へ配属となりました。旋盤などを使う機械加工なんて当時はイヤでしたね。でもお師匠さんに基礎を叩き込まれ、実際に仕事を始めたら面白くなり、異動希望は出さず、ずっと機械加工をやっています。元々機械いじりが好きだったんですね。」


仕事のやりがいとは?
大橋さん
「若い時は、難しい仕事を上手くできれば達成感があったのですが、30代半ば頃に将来を見据え、人材育成をしていかなければダメだなと思うようになりました。年齢を重ねた時に、ただ作業をしているだけではダメだと思ったのですね。そこから人材育成に力を入れるようになって、今は、育てた人が、次世代の整備士を育成している姿を見ると『おっ、ちゃんと育ったな』って思います(笑) 実作業でのやりがいも感じつつ、人が育っていくのを見るのが、今のやりがいになっています。また、職業訓練指導員の免許も取得しましたので、厚生労働省の『ものづくりマイスター』として、他の企業や工業高校などにも機械加工を教えに行くこともあります。」
注)JALエンジニアリングさんでは、「人材」の「材」の文字に「財」を当てている。人を大切にしているJALエンジニアリングさんのこだわりだ。ただ、この文章中では、通常の「人材」としてある。
垣谷さん
「試運転は、エンジン整備の最終工程です。私たちが確認をして『大丈夫です』と送り出しているものですので、そのエンジンが確実にお客さまをお運びしていることが、やりがいになっています。以前、送り出したエンジンを搭載した航空機に、自分が乗る機会がありました。その時は、安全に飛んで着陸したのを見て『やったな』って思いました。」
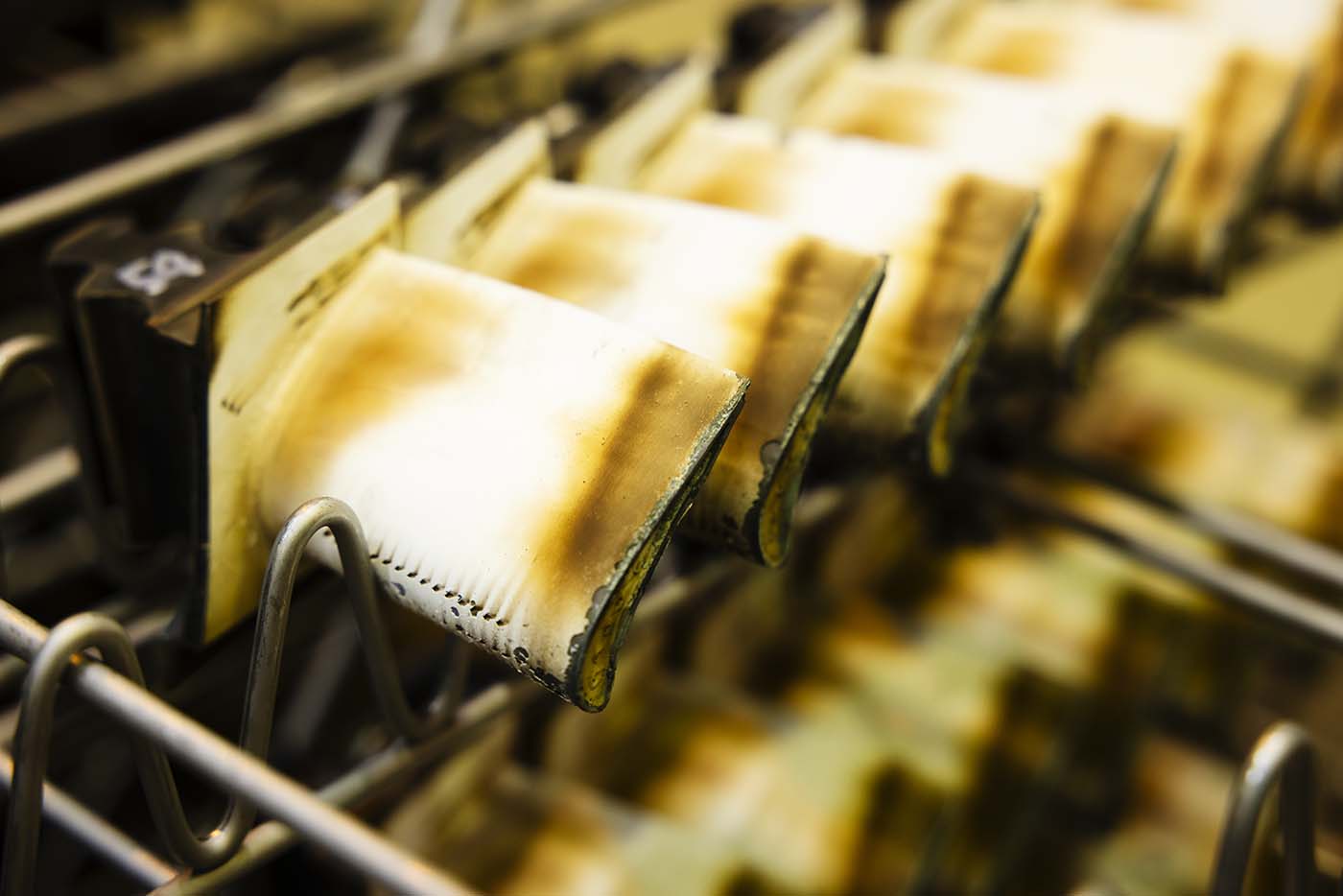
今の課題は?
大橋さん
「人材育成においては、基礎の部分が大事になってきていると感じます。単に整備士としてであれば、数年で、ある程度の作業は一人で行えるようになります。しかし、航空機部品修理の新規開発となると、どこに行っても通用するスキルを持った人が必要です。航空機整備以外の知識や経験、技能が必要なのです。また、機械加工であればマニュアルには、『OOを機械加工しろ』という指示と規定の寸法などが書いてありますが、どうやってその寸法にするのかは、整備士次第です。エンジン部品は、同じ部品、同じ材質であっても毎回同じように加工できるとは限りません。材質に合わない刃物や切削条件で加工を行えば、部品に余分な応力を与えることになってしまいます。このようなマニュアルの行間を読むことは、基礎がしっかりしていないとできません。ですから我々世代がしっかりと技能伝承を行っていかなければと思います。」
垣谷さん
「先輩方の持っている能力や知識を継承することが課題だと思っています。今、新しい機種を試運転するプロジェクトにも参加させていただいているのですが、そのような新しい取り組みをしつつ、過去から積み上げてきた経験や知識を継承できる人材になってゆかなければいけないと思っています。そのためには、エンジンだけの知識では足りず、設備や計測器などに関する幅広い知見や突発的な不具合に対する対応力も必要になってきます。ですから、試験屋として仕事をする上では、整備士以上のレベルの高さが必要になってくるんだと感じています。」
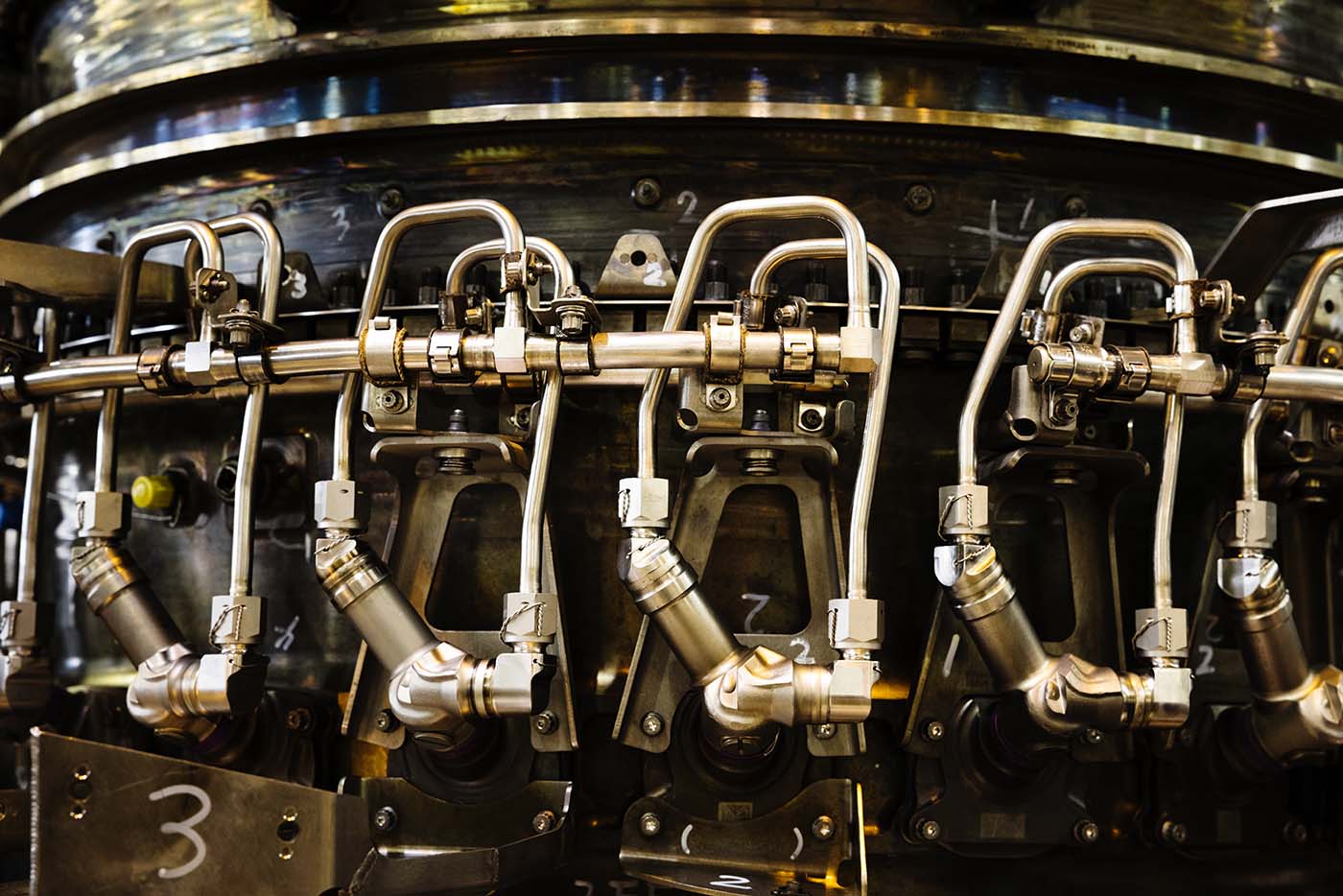
どんな整備士を目指す?
大橋さん
「航空機部品の材質は進化し続けているので、日々勉強しなければなりません。それを踏まえた上で、どんな課題や問題にも対応できる整備士になりたいですね。」
垣谷さん
「あいつに任せておけば大丈夫と言われるような整備士なりたいです。」

おわりに
若いのに、ていねいでしっかりとした語り口の垣谷さんとベテランらしい自信を持ちつつも柔和な語り口の大橋さん。インタビューの端々に「お客さまの命をお預かりしているので」という言葉が出てくるのと同様に、それぞれのお話からも常に緊張感を持ちながら仕事をしている様子が伝わってきた。
インタビューの最後に垣谷さんが、「空港で見かける整備士以外にも、多くの人が関わって航空機が飛んでるということを知ってもらいたい。」とおっしゃっていたので、少しでも伝わるといいなあと思う。
写真と文 西澤丞 インタビューは2025年5月に行いました。



