電気炉からスパーク! 鉄スクラップから新しい鉄製品を作る工場。
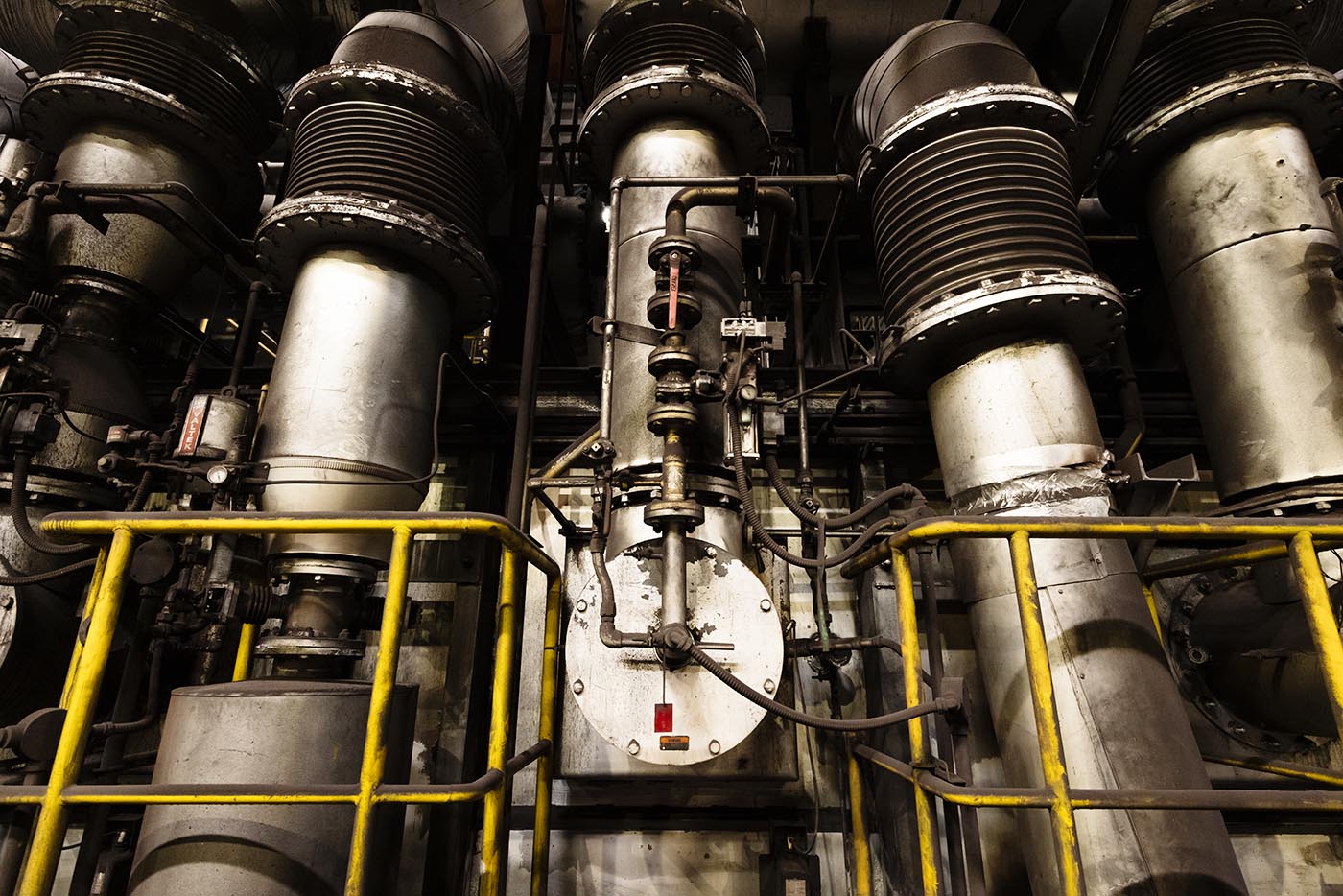
取材協力:JFE条鋼株式会社 鹿島製造所(茨城県神栖市)
はじめに
「電気炉って、興味ありますか?」
そんな言葉に誘われてお邪魔したのは、鹿島臨海工業地帯の一角にあるJFE条鋼株式会社。鉄スクラップを溶かして、建設資材や機械の部品などに使われる新たな鉄製品を作っている工場だ。
いざ、現場へ
小雨がぱらつく中、まだ夜が明け切らないうちに宿を出て、現地に向かう。工業地帯特有のまっすぐな道を走ってJFE条鋼さんに着いたのは、午前5時。集合時間が早いのは、電気炉が稼働する時間の都合だ。電気を大量に使う電気炉の稼働は、電気の供給に余裕のある夜間に行われていて、朝5時に行けば、最後の作業を撮影できるのだ。だから、着いたらすぐに、電気炉で鉄スクラップを溶かしている様子から撮影することになった。
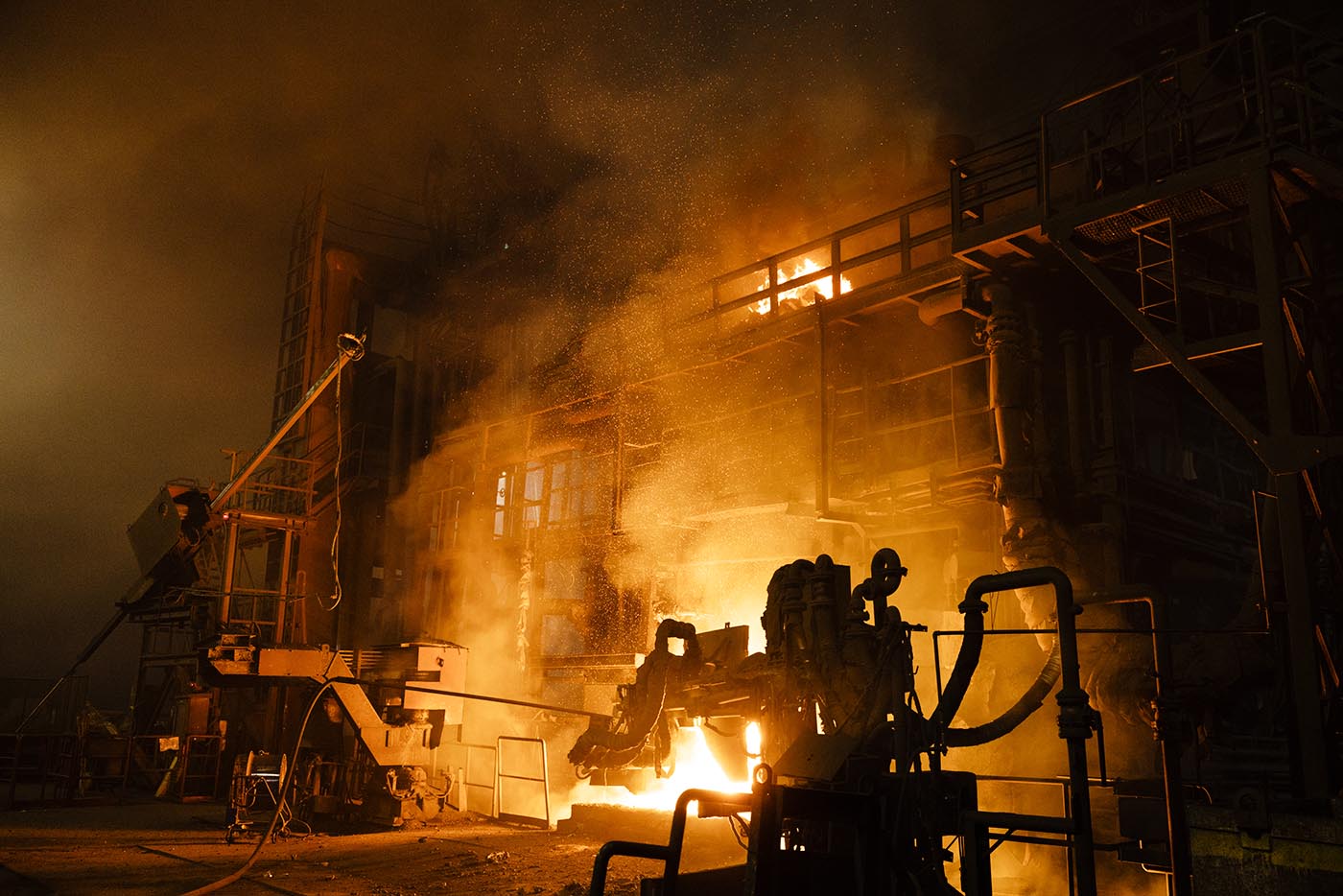
最初に撮ったのが、この写真。もうすでにバリバリといったすごい音を立てながら鉄スクラップの溶解が始まっていた。写真では見えないが、電気炉の中に鉄スクラップを入れ、そこにグラファイト製の電極を差し込んでいる。
と、こんな感じで撮影が始まったわけだが、撮影は工程順に行なっているわけではないので、そのまま並べてしまっては、何が何だか分からなくなってしまう。そこで、ここからは、工程に合わせて写真を再構成し、それに合わせて文章も書いてゆこうと思う。
製鋼工程
製品を作る工程は、上工程の製鋼と下工程の圧延に分かれているので、まずは、製鋼に関する部分を、製鋼統括の木内博一さん(57歳)に聞いてみた。それによると、製鋼の工程は、以下のような流れになっている。
1)原料の受け入れ
2)配合
3)溶解
4)精錬
5)連続鋳造
6)切断
じゃあ、写真と一緒に見てゆこう。
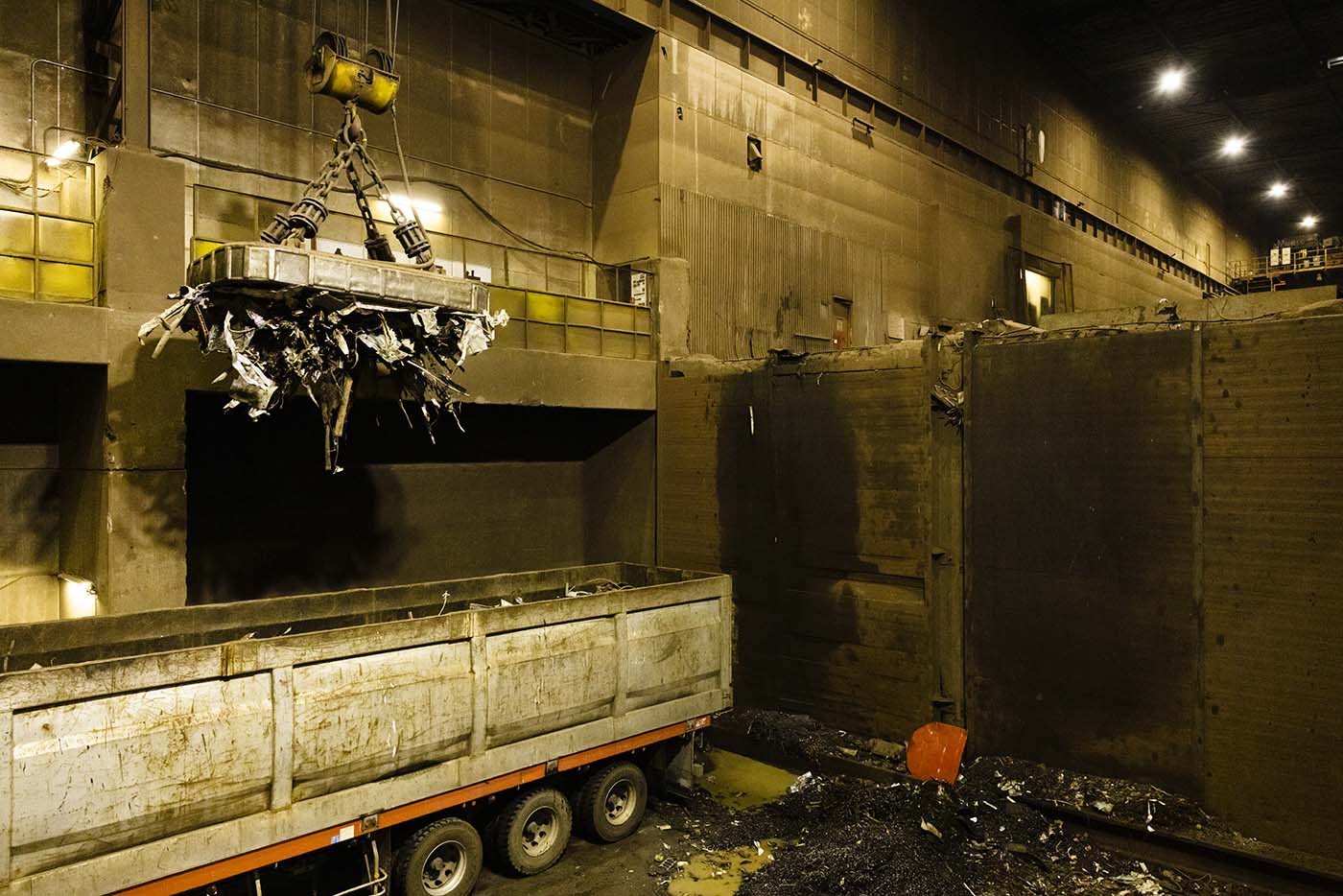
原料の受け入れ
業者さんが運んで来たスクラップを、電磁石のついたクレーンで原料(スクラップ)ヤードに運ぶ。原料には、不純物の混ざり具合などによって複数の等級があって、等級を見分けるのは、クレーンのオペレーターさんの仕事だ。木内さんが、等級の具体的な内容についても教えてくれたが、あまりに専門的すぎて、僕自身理解できなかったので、割愛させていただく。
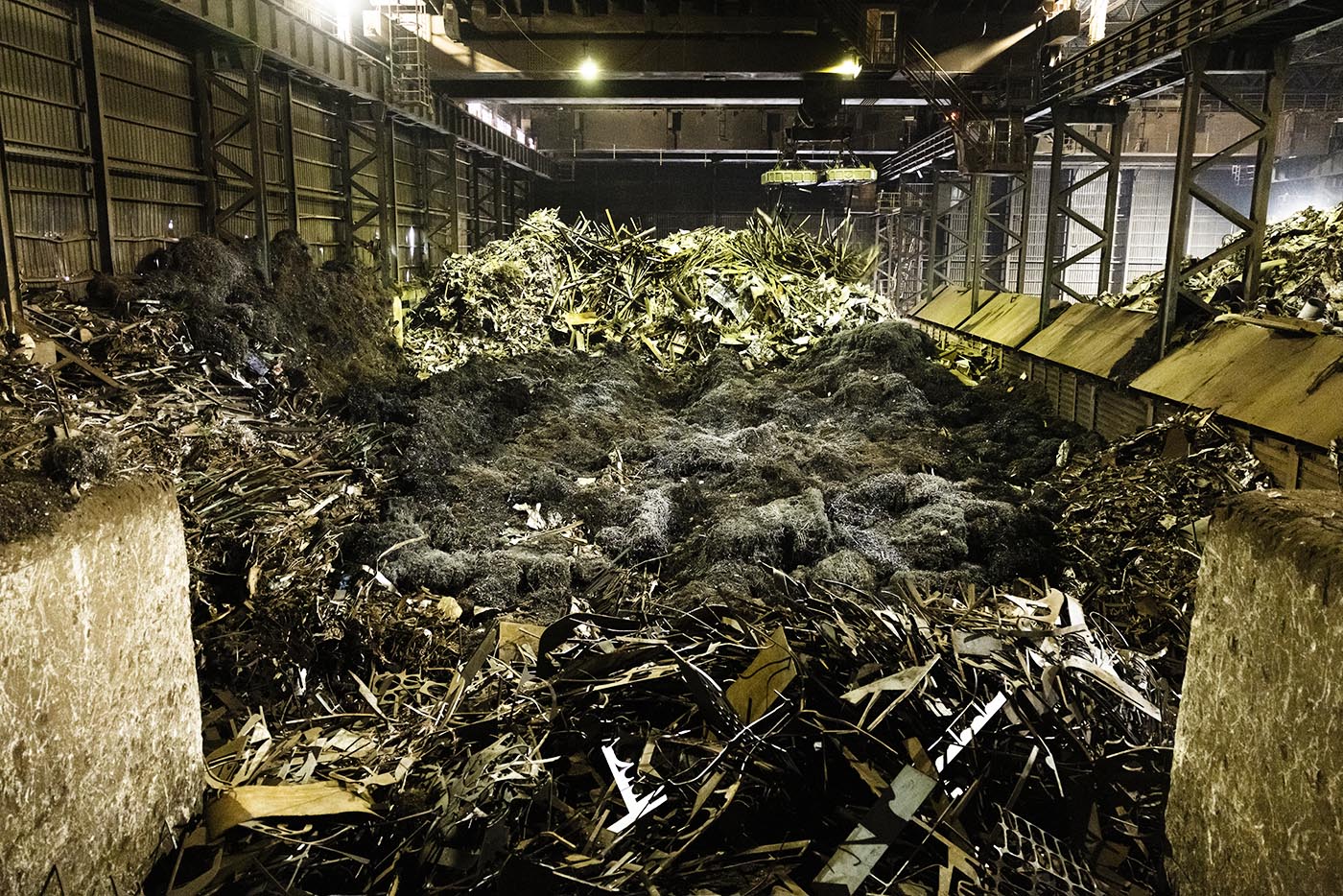
原料(スクラップ)ヤードは、こんな感じ。スクラップの種類ごとに分けて保管されているのが、お分かりになるだろうか?
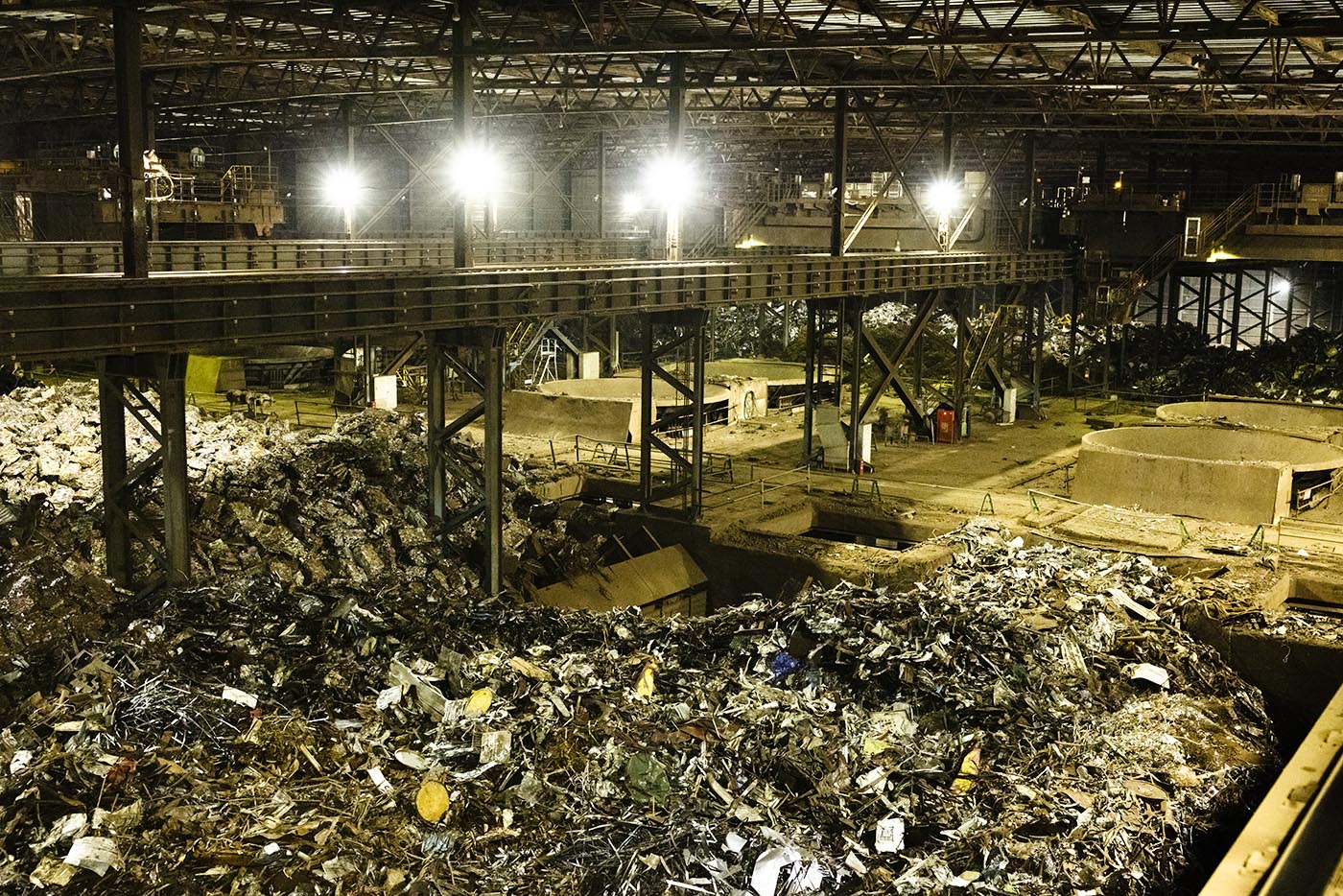
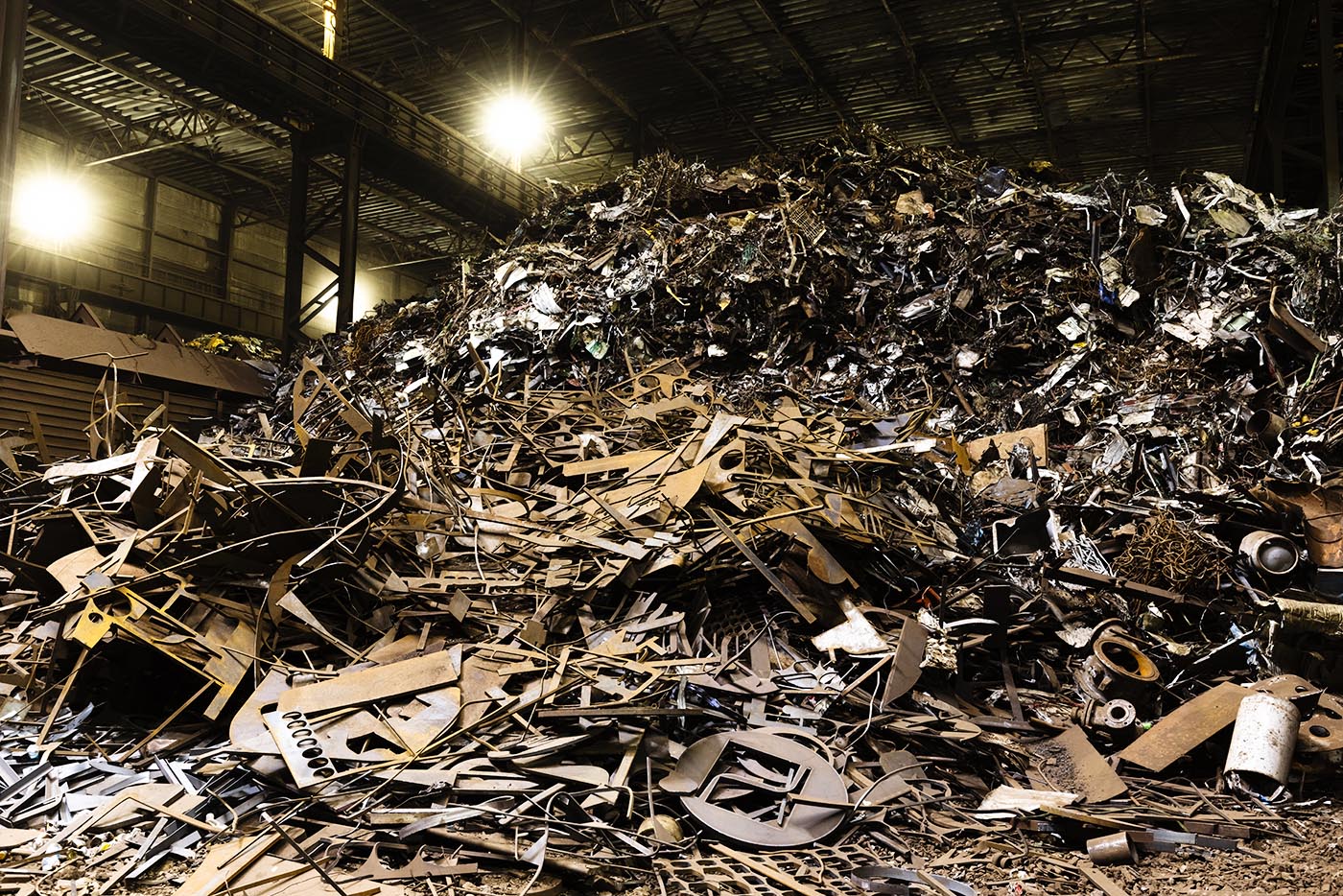
等級ごとに分けて保管されていたスクラップを、うまく配分して製品に適した鉄になるようにしている。なお、スクラップを選別するのは人力だが、溶かす時に必要なスクラップを集めるのは自動で行われる。
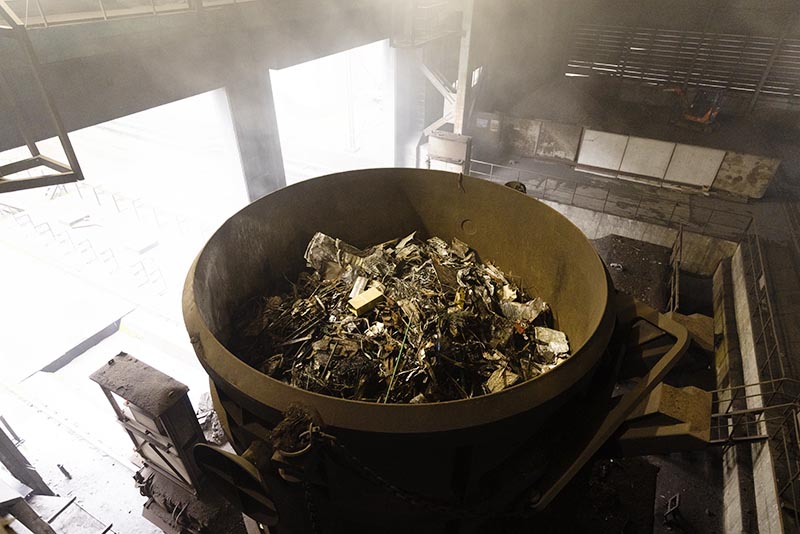
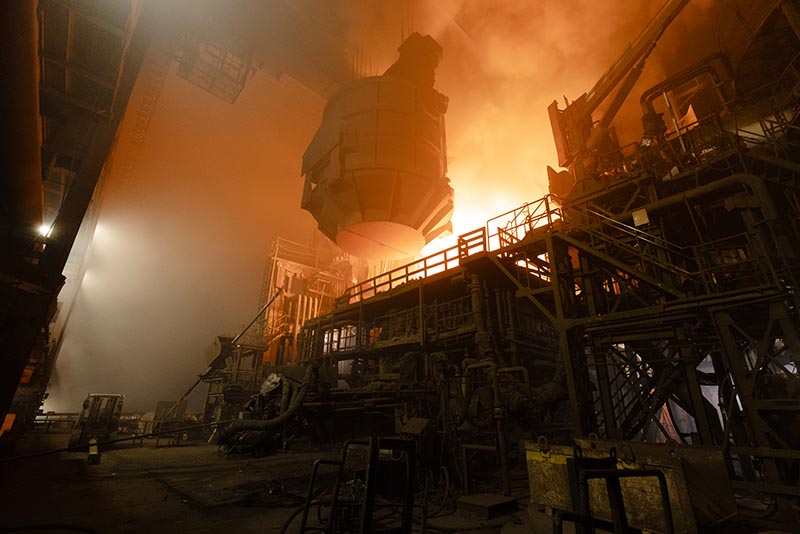
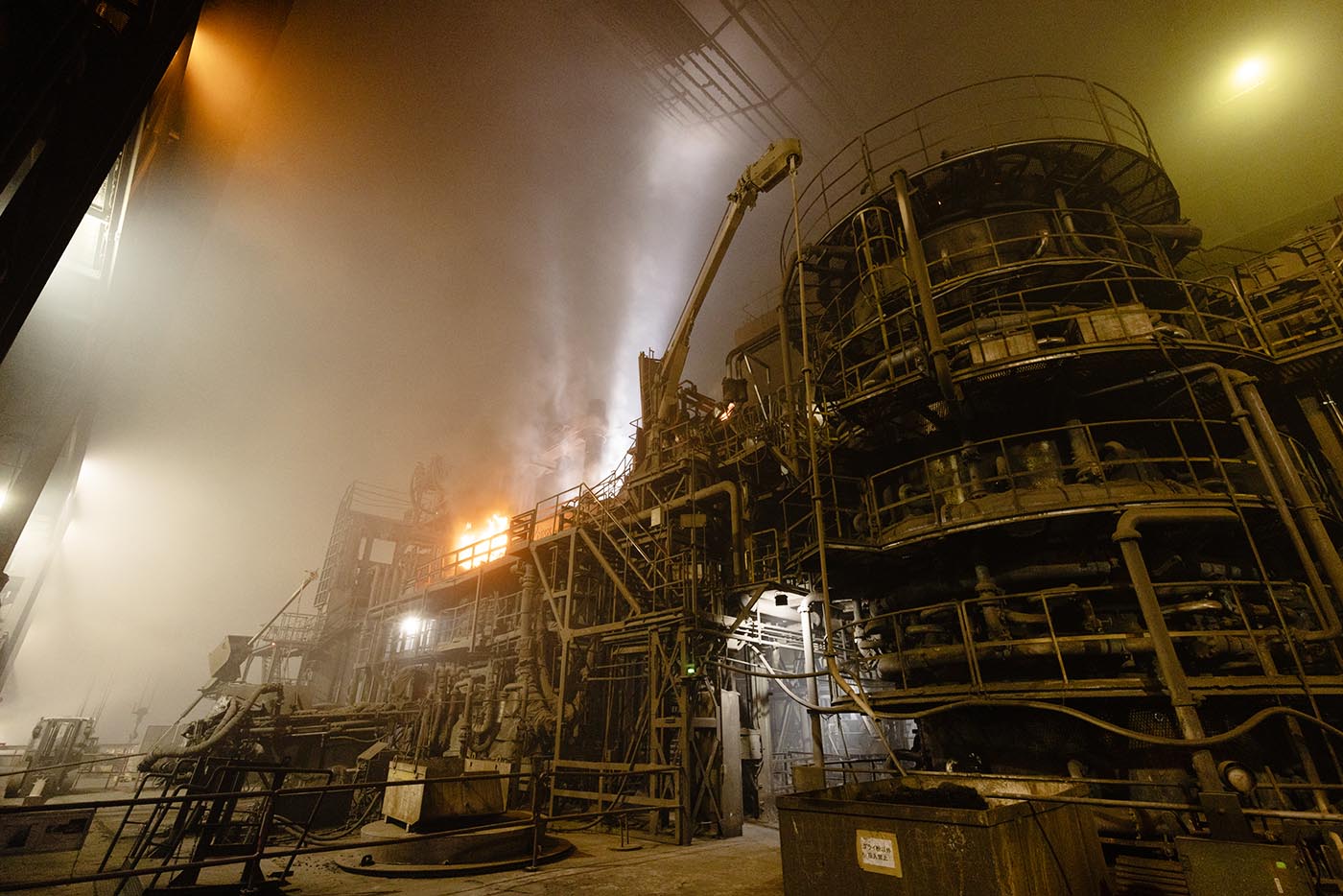
溶解
電気炉には、3回に分けてスクラップを投入するのが基本だが、場合によっては2回にすることもある。電気炉で電力を使う時間帯は、電力会社との契約で夜間(22時から7時の間)となっているので、電気炉の稼働時間が延びて昼間の時間帯になってしまうと超過料金を払わなければいけなくなってしまう。それを避けるため、投入を2回にして時間を短縮することもあるという。
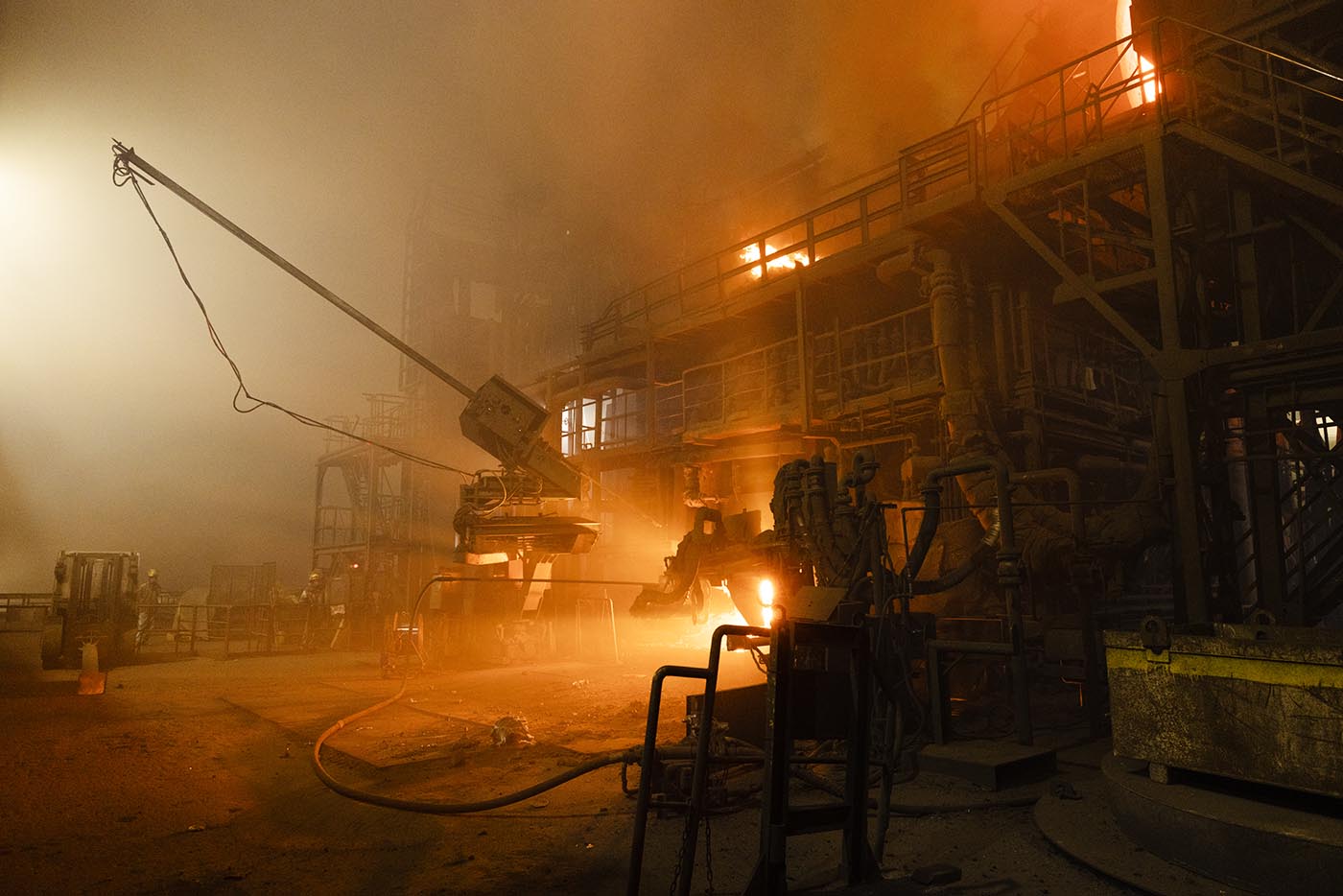
鉄が溶けたら、棒状のものを差し込んで、成分を調べるためのサンプルを取る。
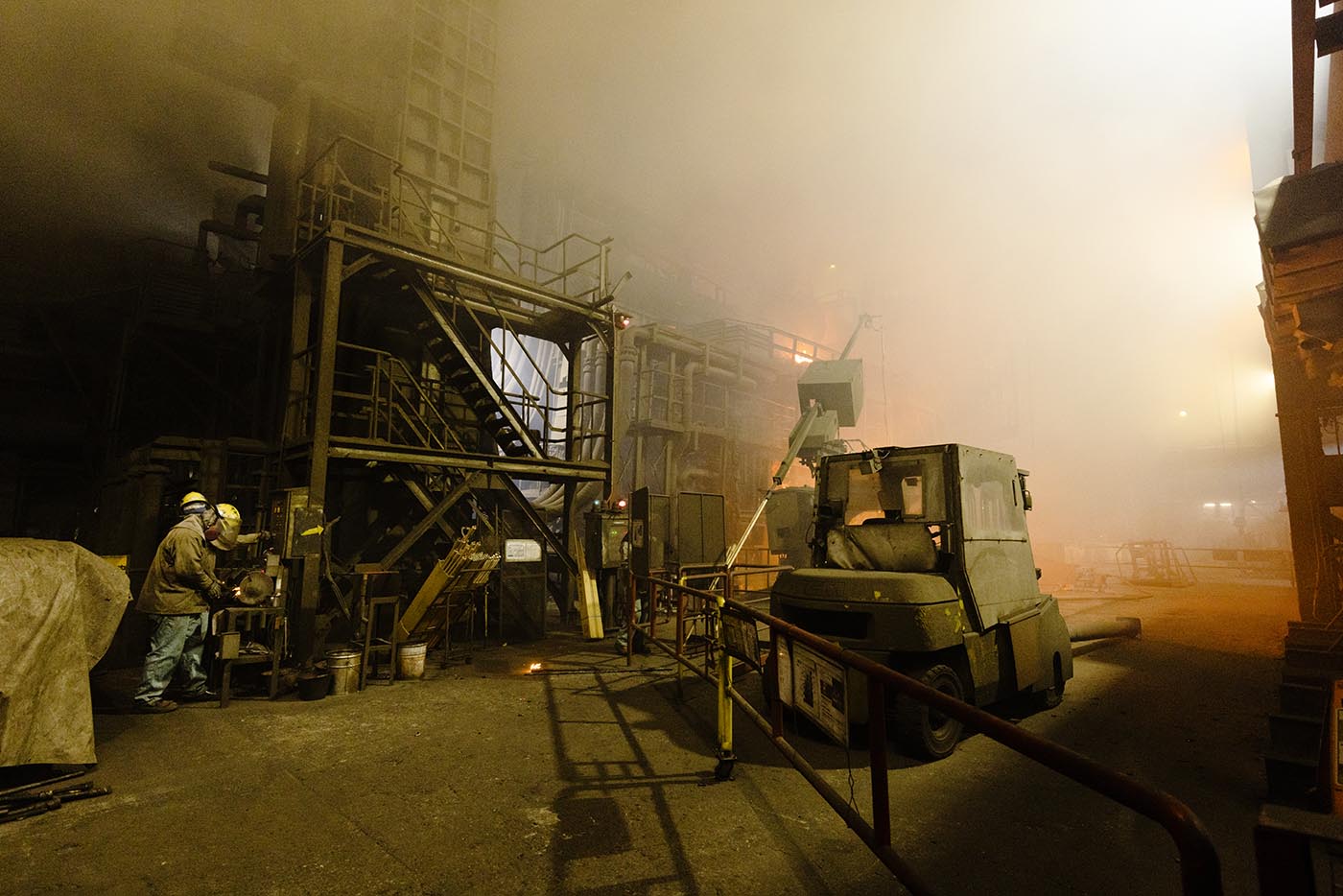
サンプルを取ったら、グラインダーで削る。グラインダーで削ったときの火花によって、鉄に含まれるカーボンの量がわかるのだ。ここでの成分確認は、あくまで目安で、詳細な成分については、分析室で調べる。
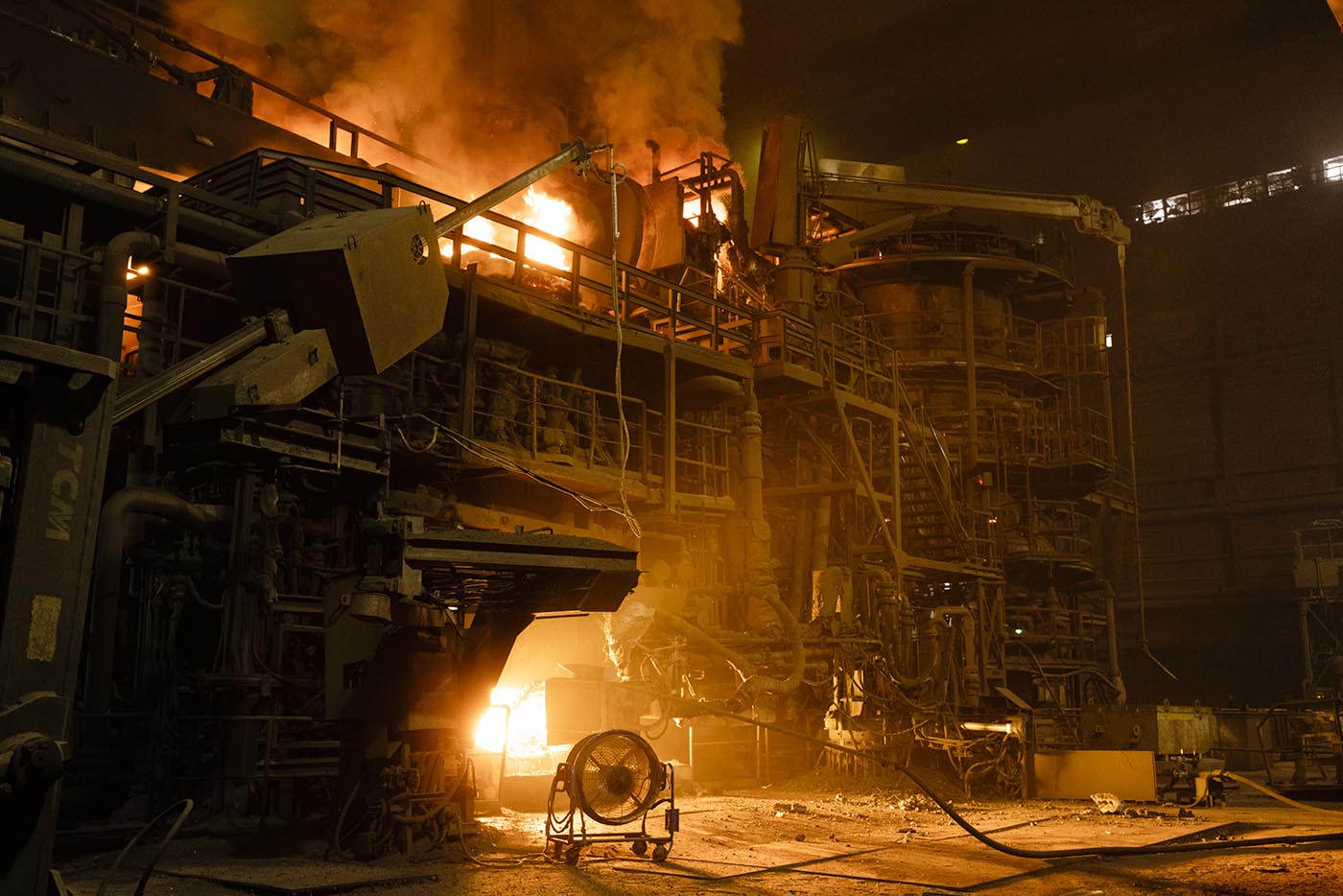
作業員さんたちは、サンプルを取るとき以外は、操作室にいるので、稼働中の電気炉の周りは基本的に無人だ。この写真には、なんだか可愛い扇風機が写っているが、これは、後の作業で使うもので、これを使って電気炉を冷やしているわけではない。
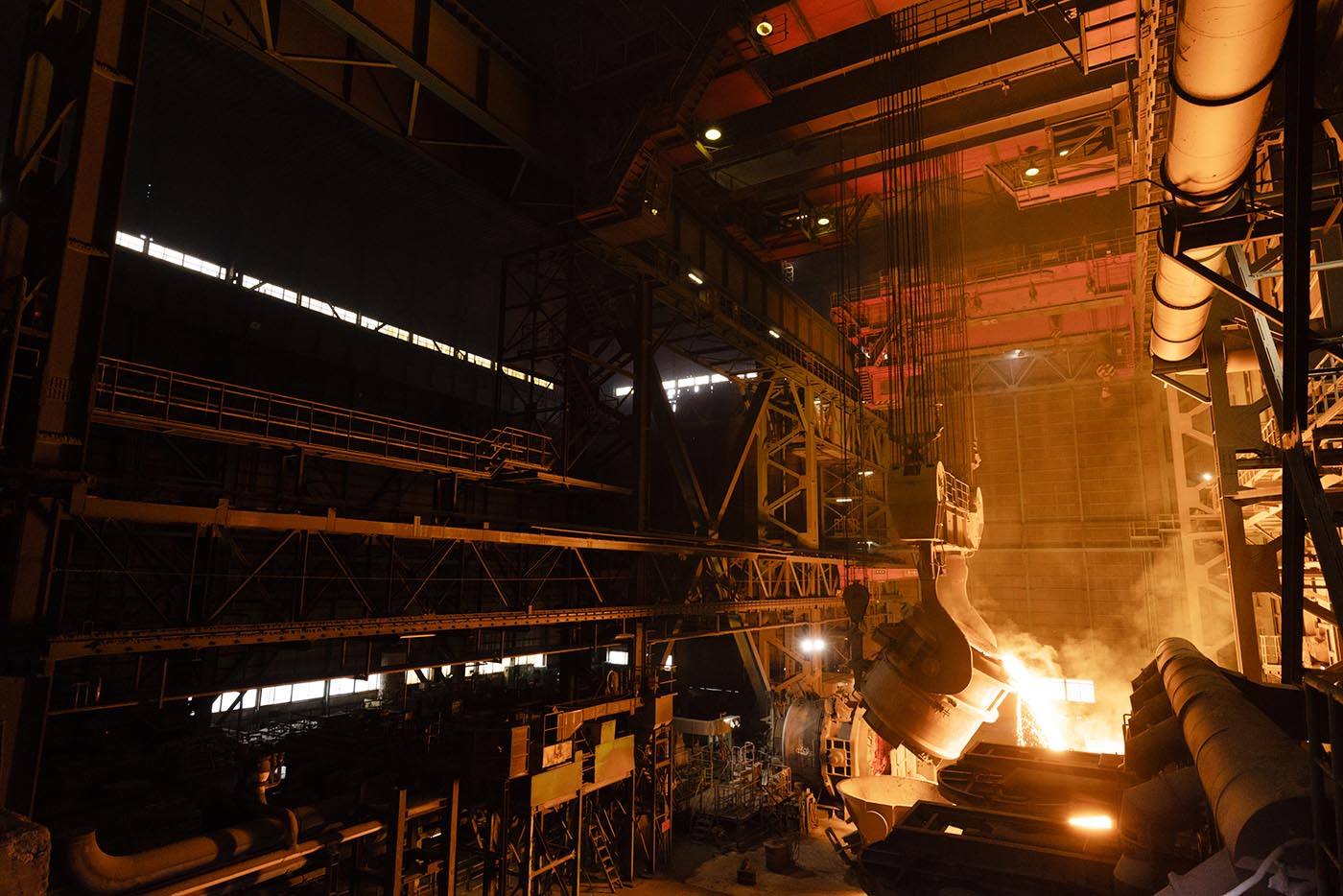
溶けた鉄の上澄み部分を捨てている様子。上澄み部分は、スラグと呼ばれ、道路を作るときの路盤材として販売することもある。
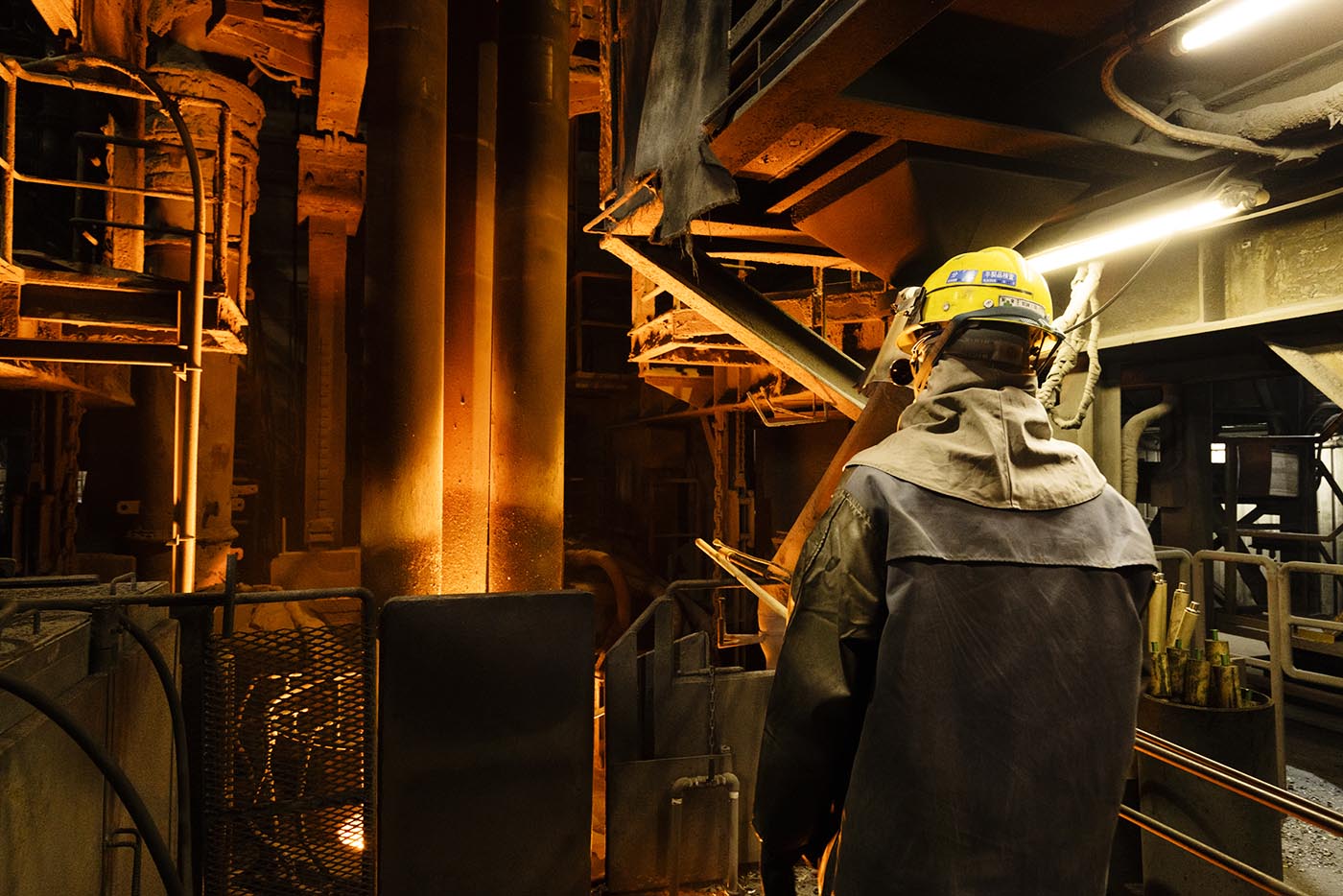
精錬
溶けた鉄の成分を調整している様子。材料にスクラップを使っているため、溶けた鉄は、毎回、成分の違うものになってしまう。そこで、シリコンやマンガン、バナジウムなど、複数の材料を使って成分を調整する。安価な原料でも使いこなさなければいけないので、臨機応変に判断するのが難しいという。
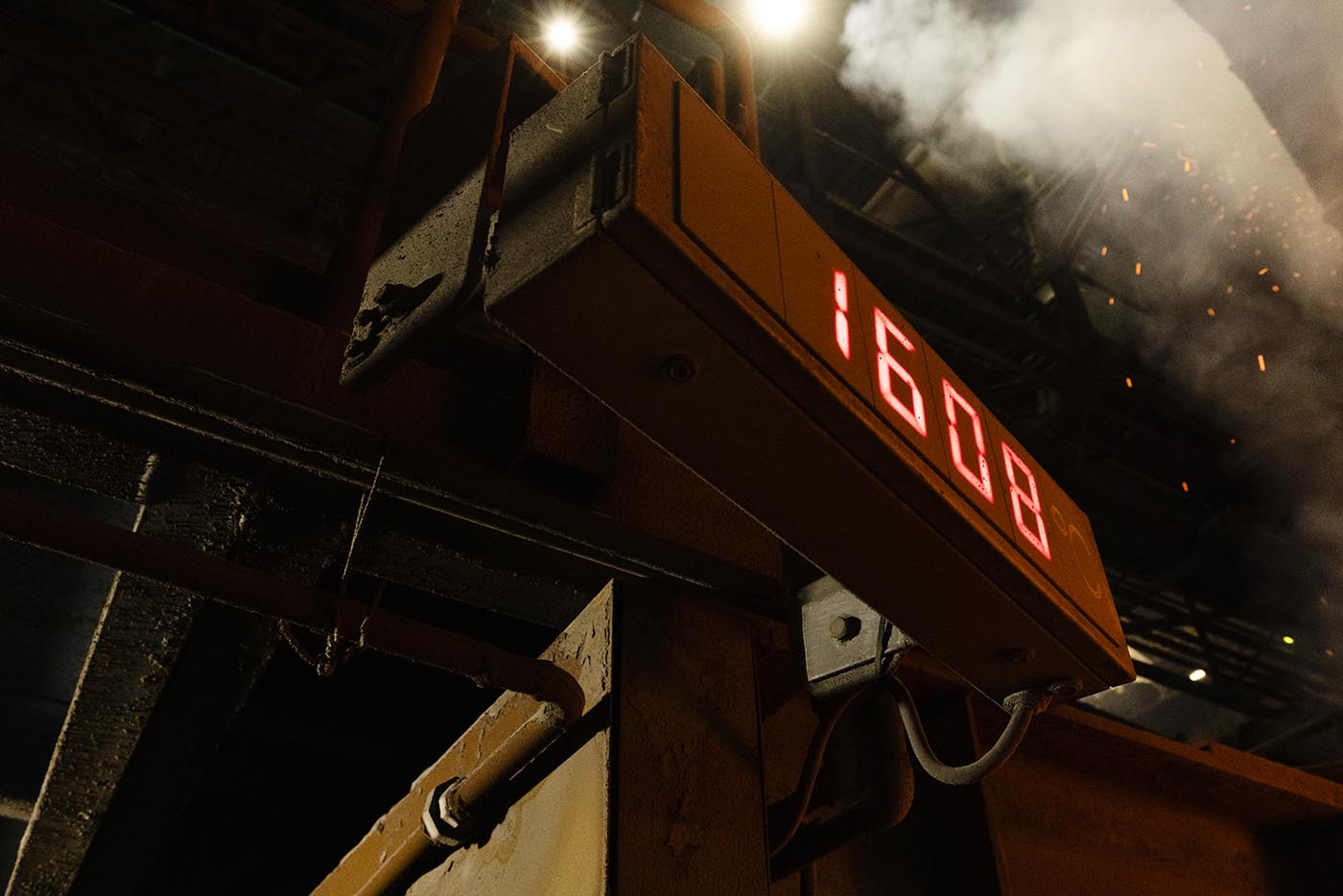
成分を調整する時の温度は、1600度くらいだね。ベテランさんは、鉄の色や鍋の中の様子、出ている蒸気の色なんかで、溶けた鉄が、いい状態なのか悪い状態なのかの判断がつくらしい。この辺りは、経験だけではなく、センスが重要だとのこと。
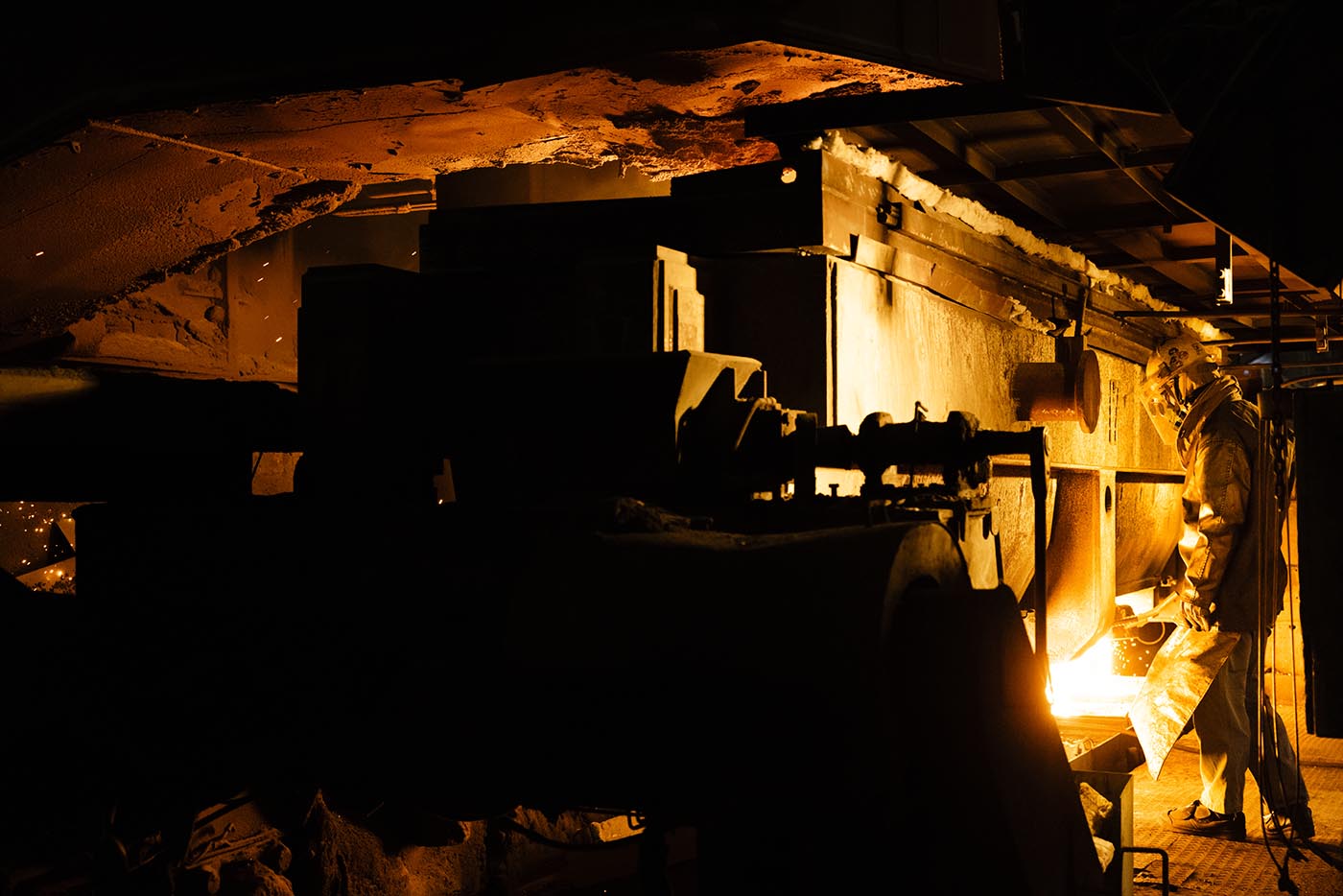
連続鋳造
成分の調整が終わったら、製品の形にする前に一度、棒状に固める。その方法は、溶けた鉄を器(タンディッシュ)に注ぎ、その器の底の部分から、ところてんのように鉄を出してゆくイメージだ。この器からは、一度に5本出てくる仕組みになっている。写真に写っている作業員さんは、受け口に溜まる不純物を取り除いたり、きちんと流れているかどうかをチェックしている。
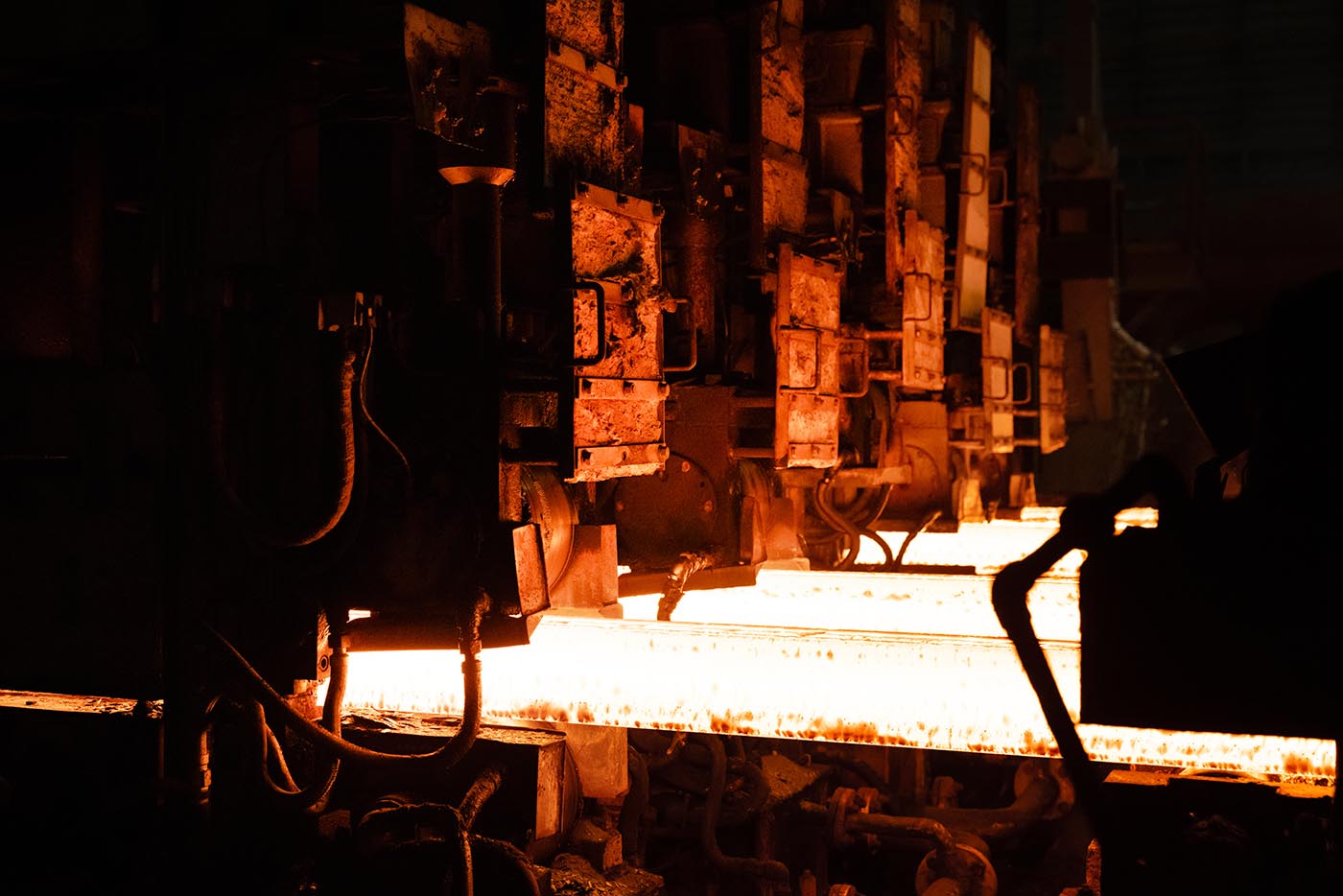
さっきの所では、まだ液体だった鉄が、棒状の塊になって出てきた。
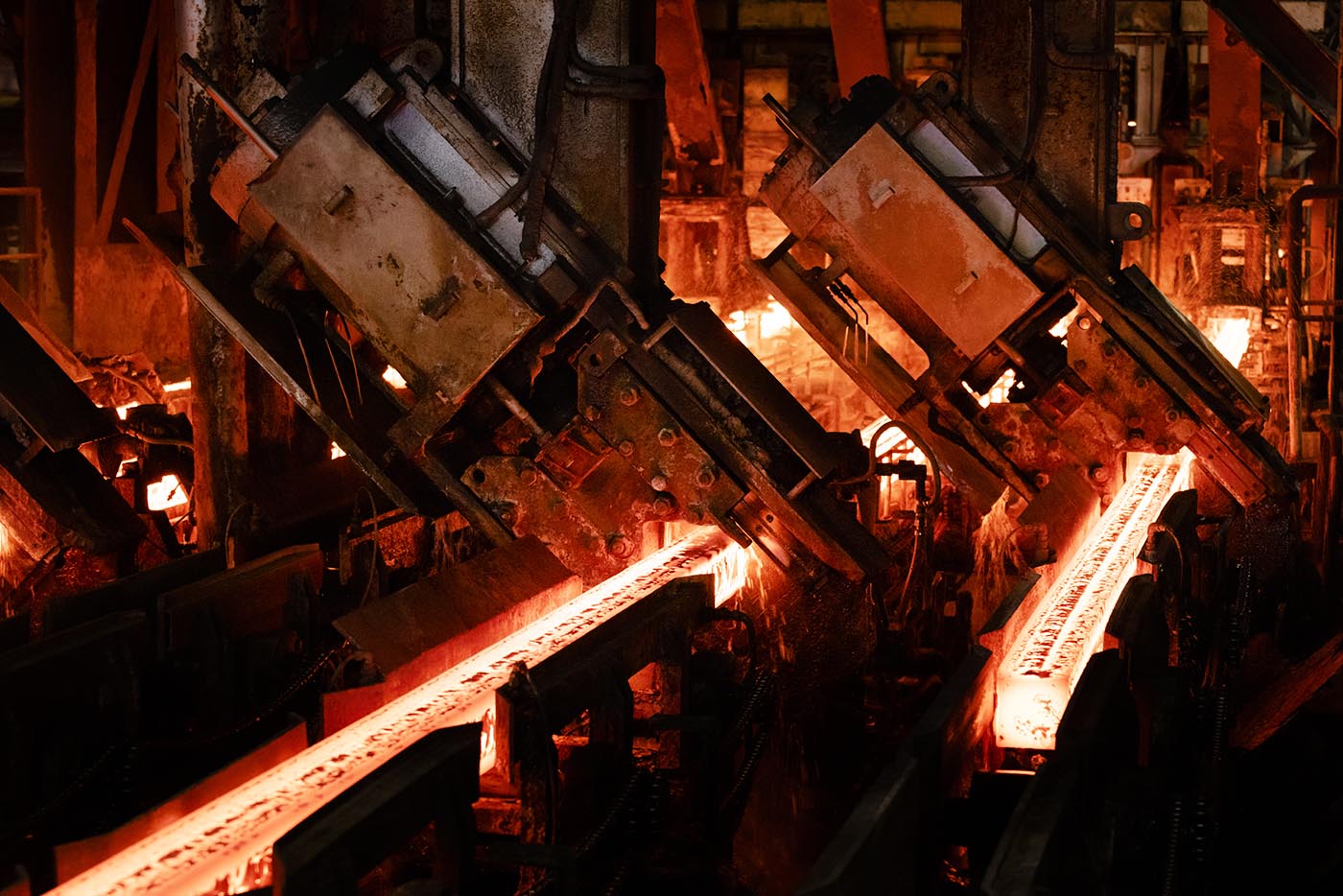
切断
鉄の塊は、大きなペンチのような機械で、6mから11mくらいの長さにカットされる。今回の撮影では、これを撮っている時が、一番熱かった。まあ、普段は、人がいない所だけどね。そうそう、切断後の棒状の塊はビレットと呼ばれているよ。
製鋼の工程は、ここまでだけど、溶けた鉄を運んでいた鍋の整備作業を撮影できたので掲載しておく。
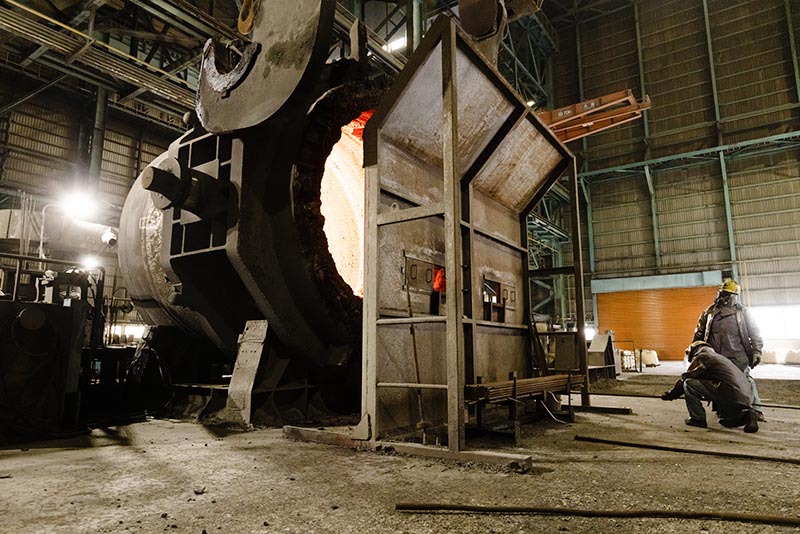
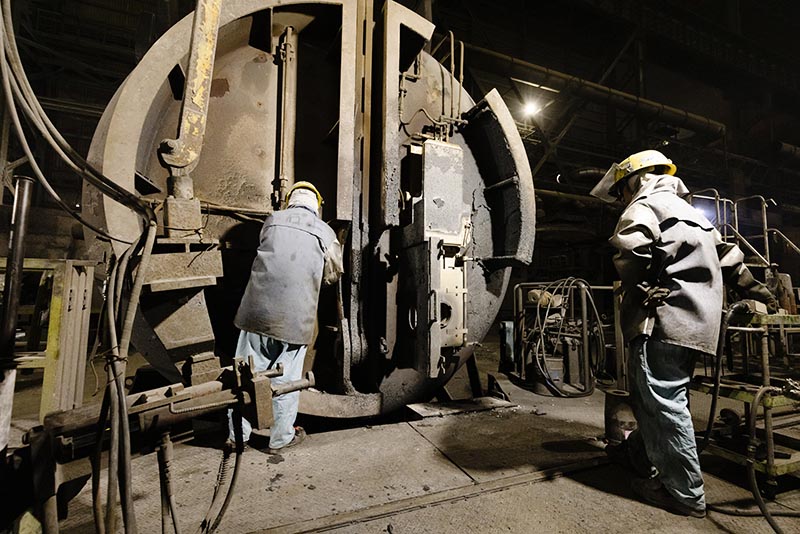
圧延工程
さて、次は、圧延の工程だ。圧延に関しては、圧延統括の木内啓治さん(52歳)に教えてもらった。圧延の主な工程は以下の通りだ。
1)加熱
2)圧延
3)冷却
4)矯正
5)切断
6)検査
順番に見てゆこう。
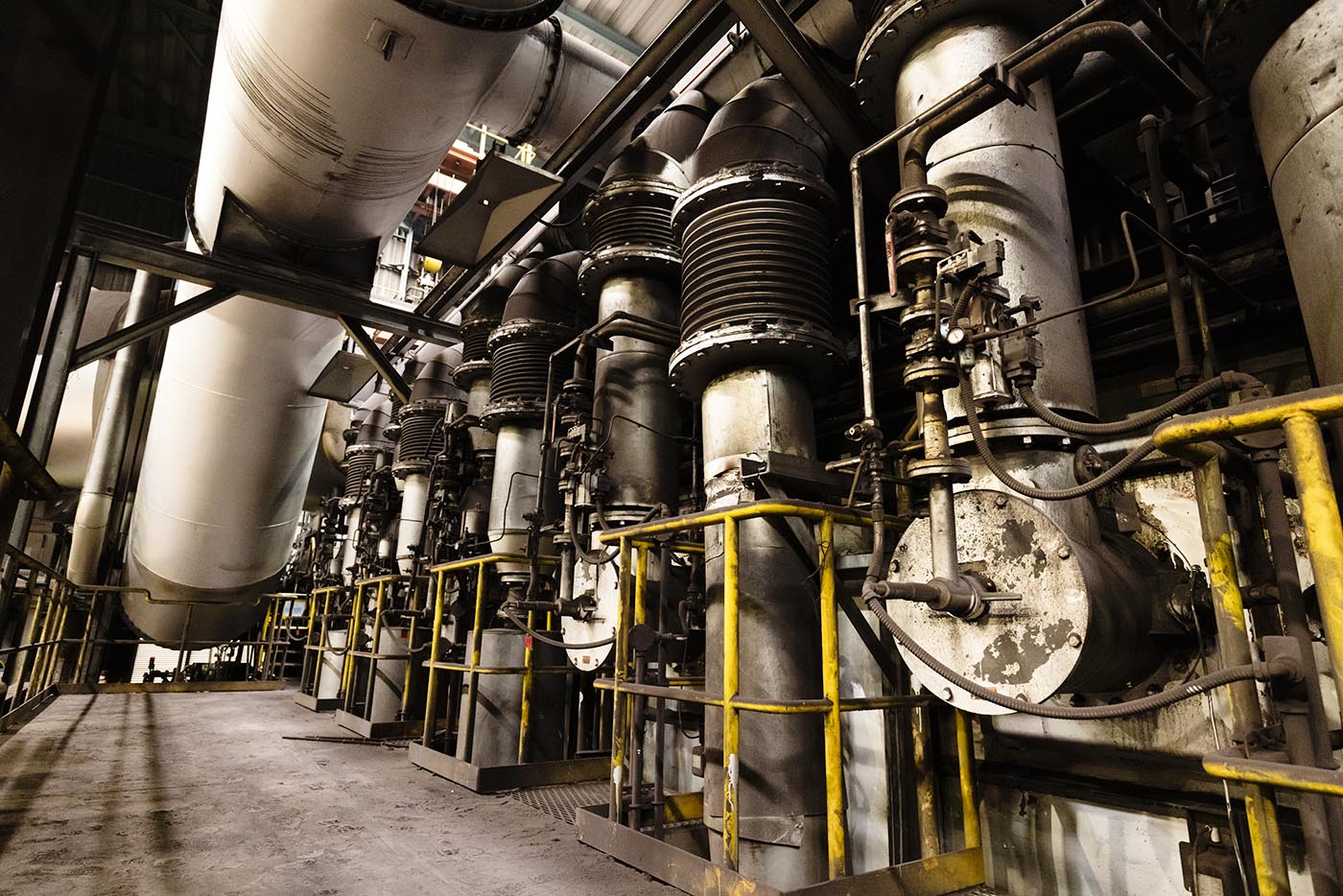
加熱
ビレットを加熱するための炉の外観は、こんな感じになってる。この炉の中で、1時間半くらいの時間をかけて、950度〜1050度くらいまで加熱する。温度に幅があるのは、何を作るのかによって温度が違ってくるからだ。また、燃料費を抑えるために、製鋼の工程から冷める前のビレットを持ってきて加熱することもあるそうだ。
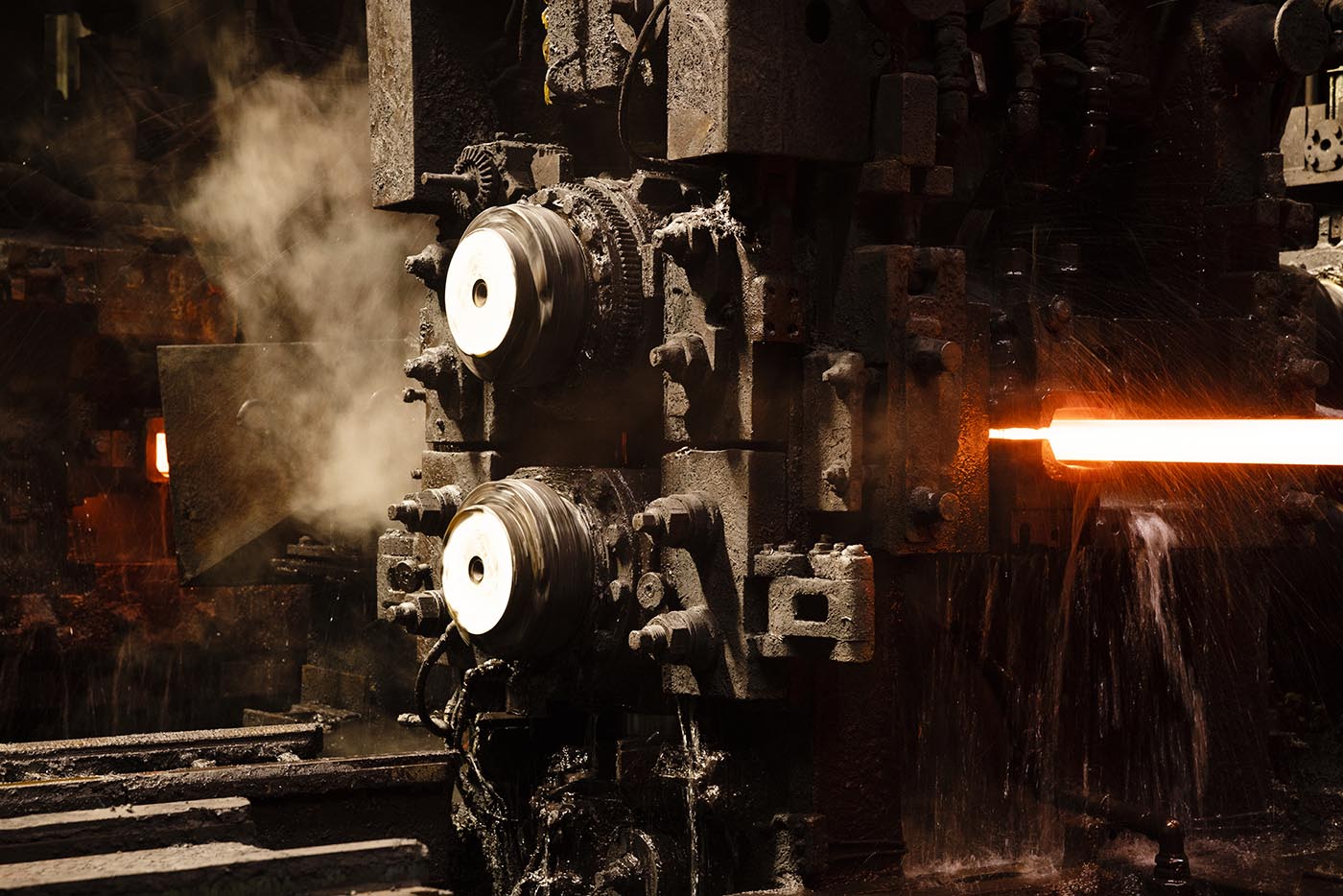
圧延
加熱の次は、圧延だ。圧延機は全部で18台あり、作る製品によって使う圧延機の数が違ってくる。この日は、16台の圧延機が使われていた。圧延機は、ロール部分を交換することで、様々な製品を作ることができるようになっている。
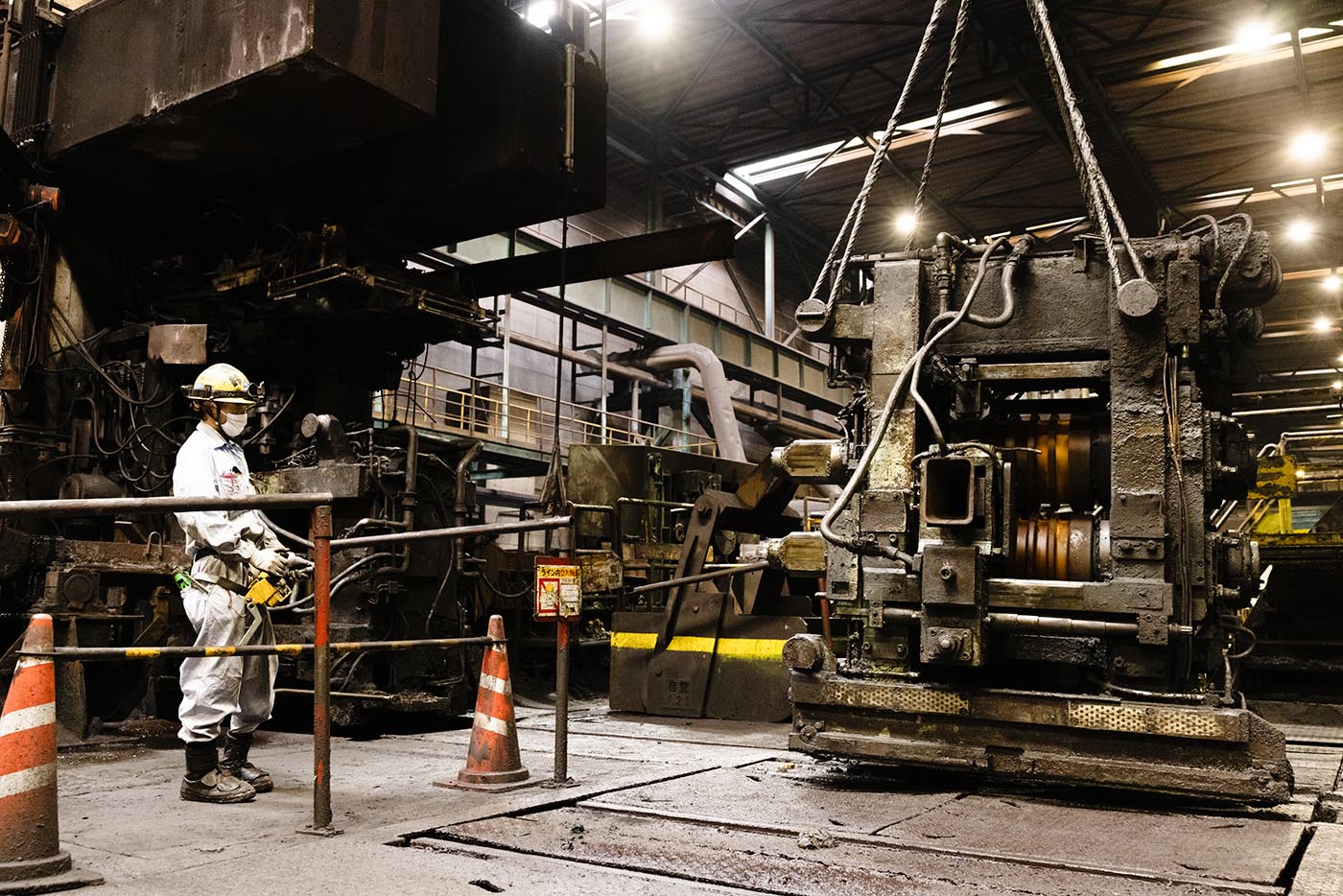
ロール部分は、写真のように上下が一体となった状態で交換できるようになっている。作る製品のサイズが17種類ほどあるので、ものすごい数のロールがあるってことだ。なお、製品を作り分けるための段取り替えは、毎日のように行われていて、1回につき、1〜2時間くらいかかる。
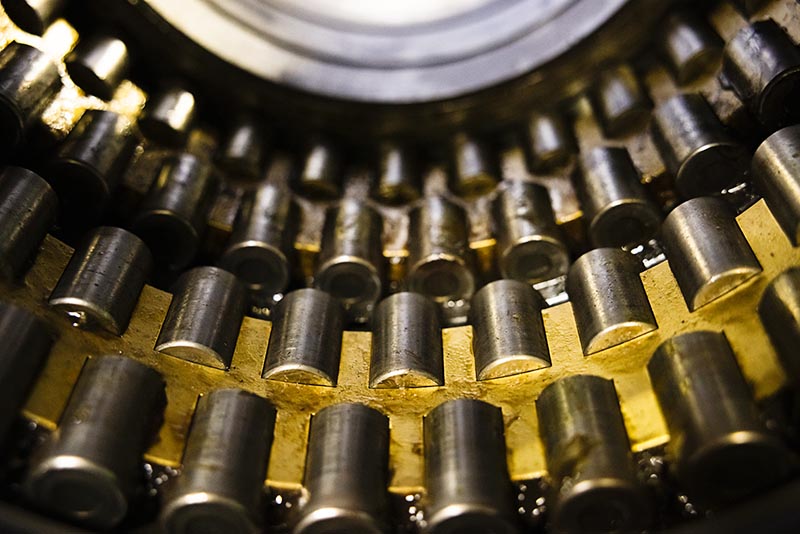
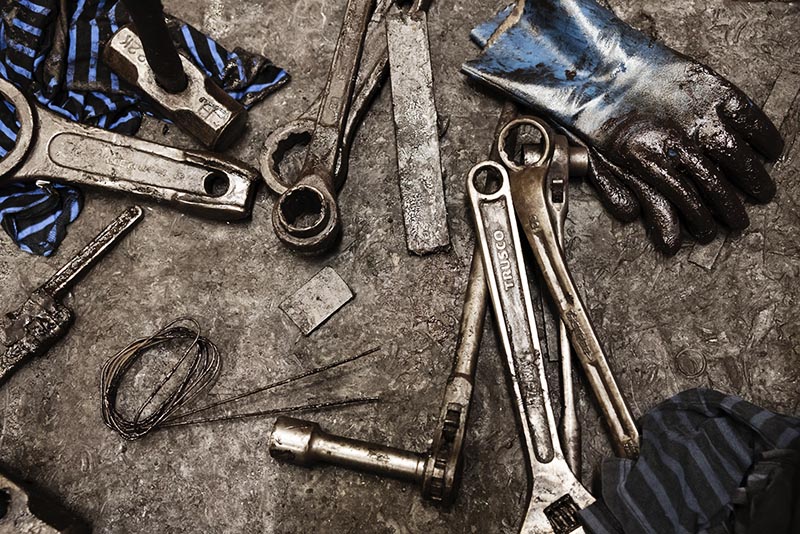
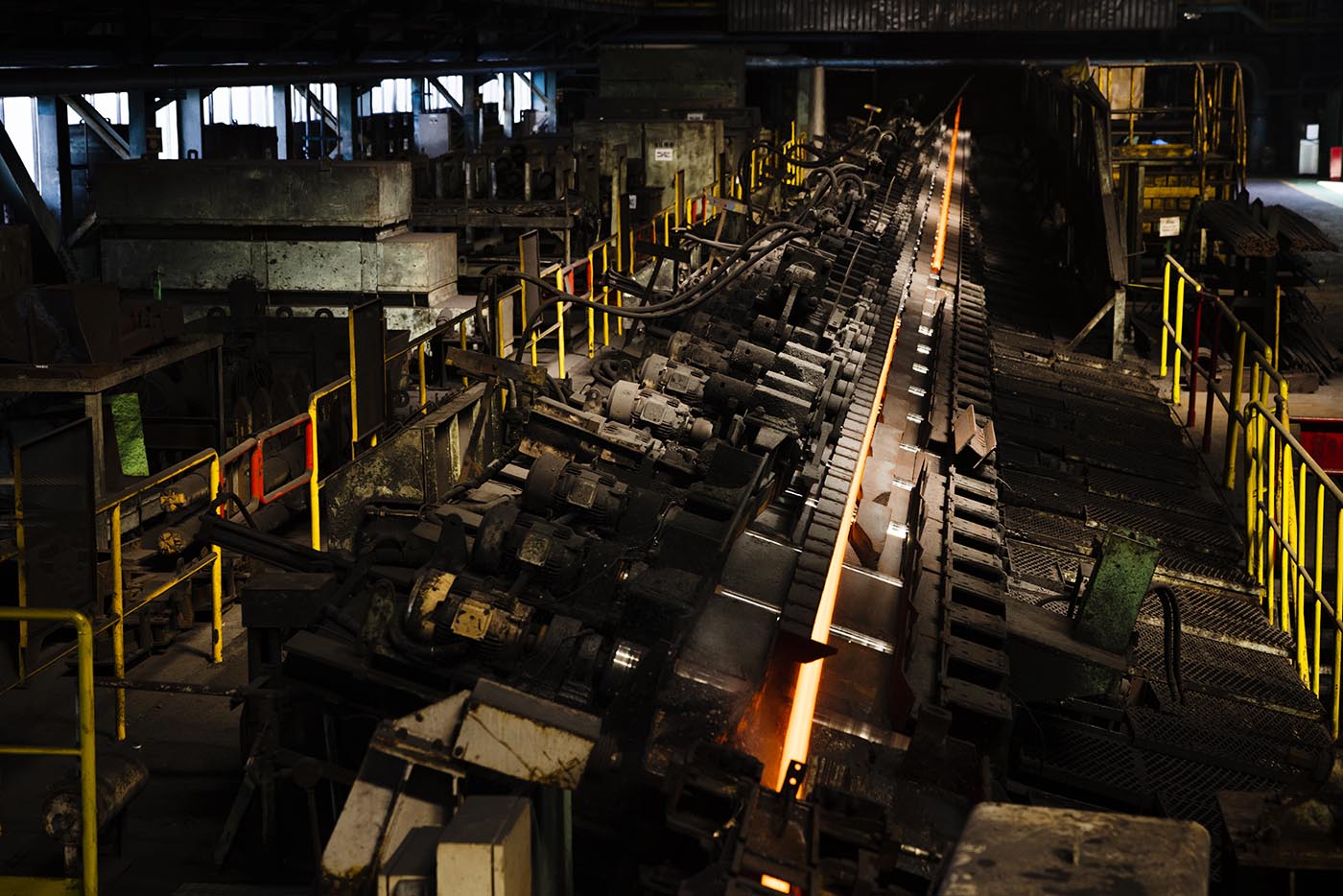
圧延機から出てきた材料は、まだ真っ赤な状態だ。ここでは、搬送中、同じラインに入らない様に振り分けている。この日は、10mのビレットを、134mごとに分割しながら402mまで圧延していた。
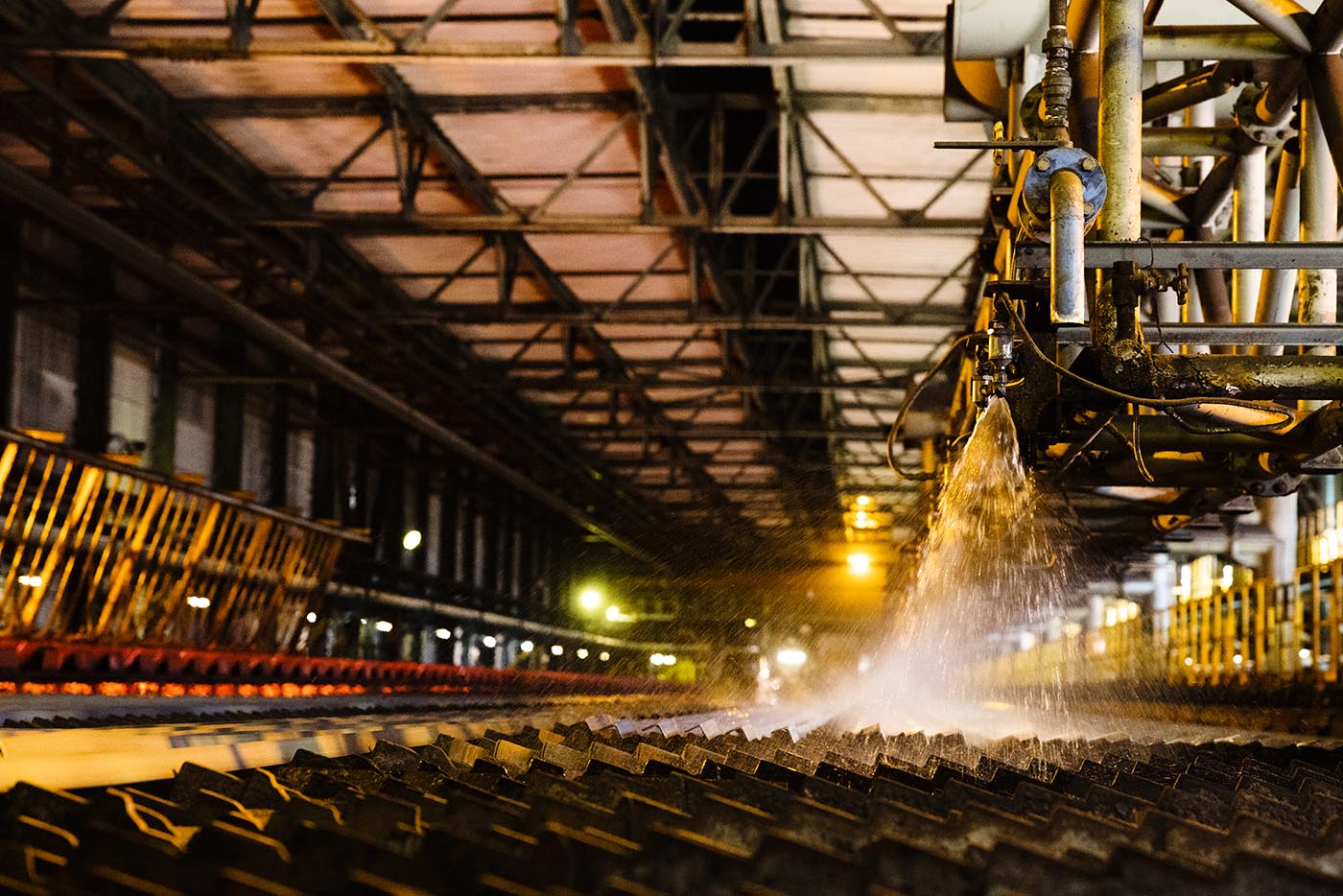
冷却
ここは、圧延した材料を冷却するための場所。床全体が、画面の左側から右へと移動してゆく。
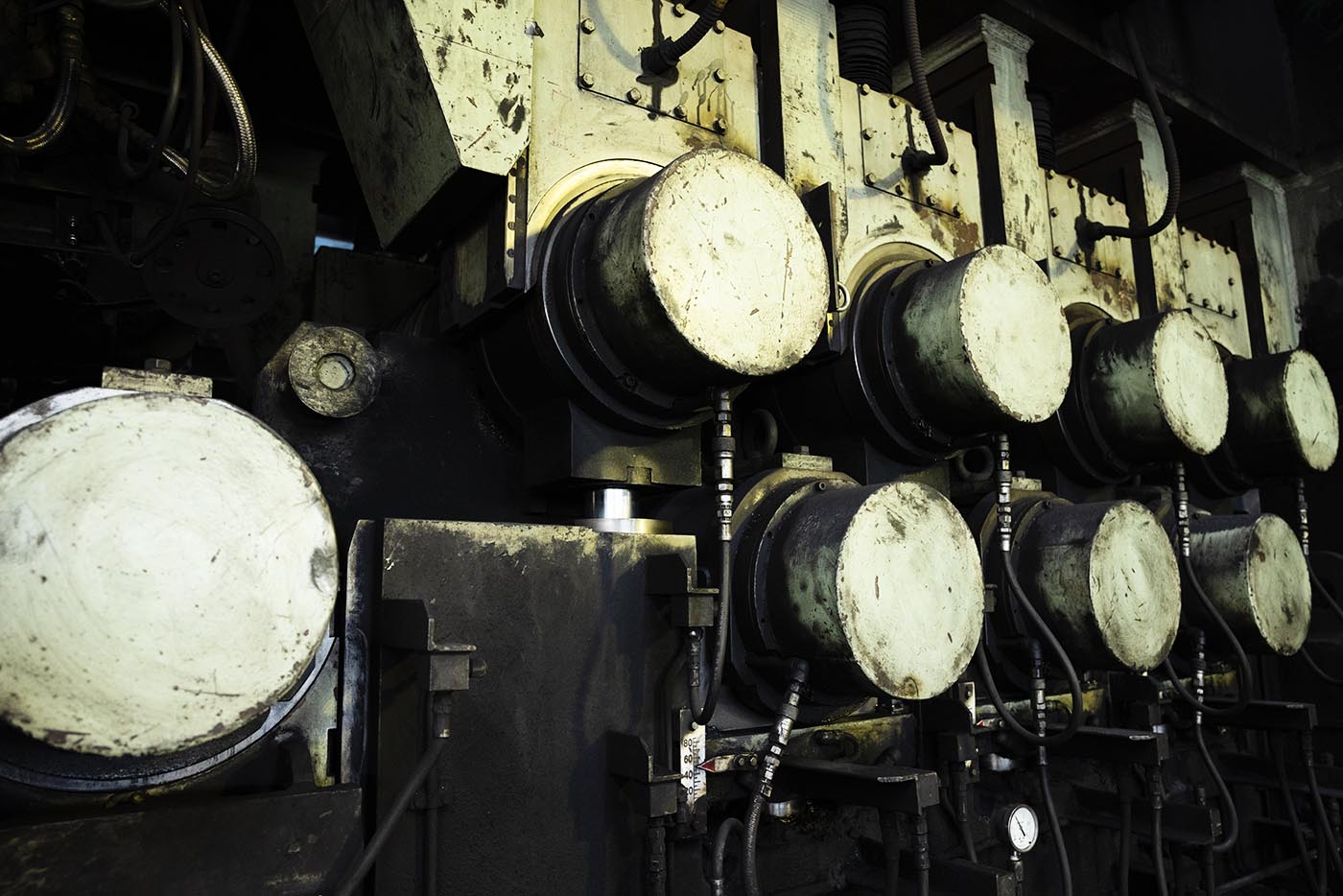
矯正
冷却が終わったら、今度は、矯正機にかけて歪みを取る。それと同時に、半分の長さ(この日は、67m)に切断する。
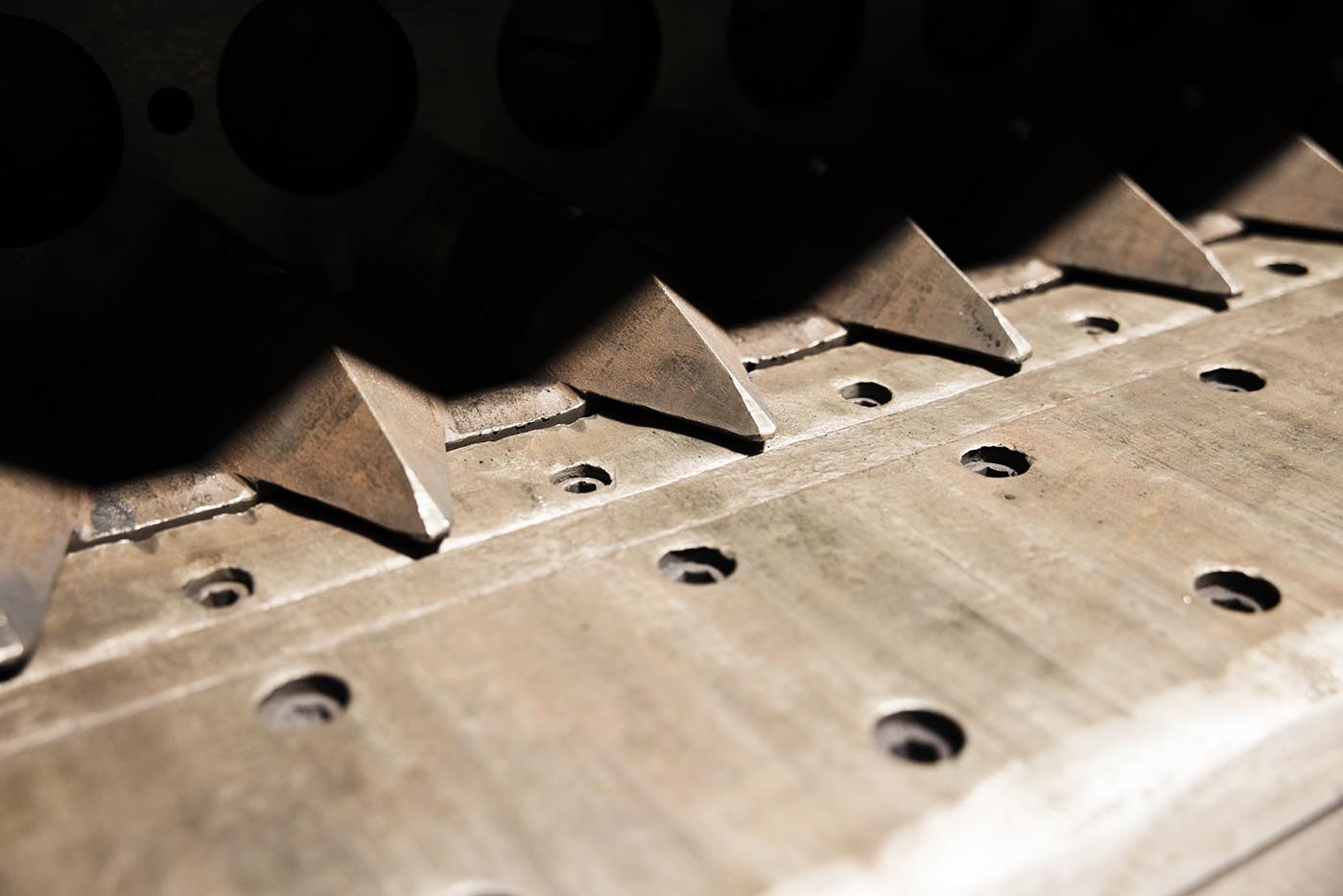
切断
矯正が終わったら、製品の長さに切断する。写真は、切断機に取り付ける歯の部分。製品の長さは、5.5m〜12mだ。
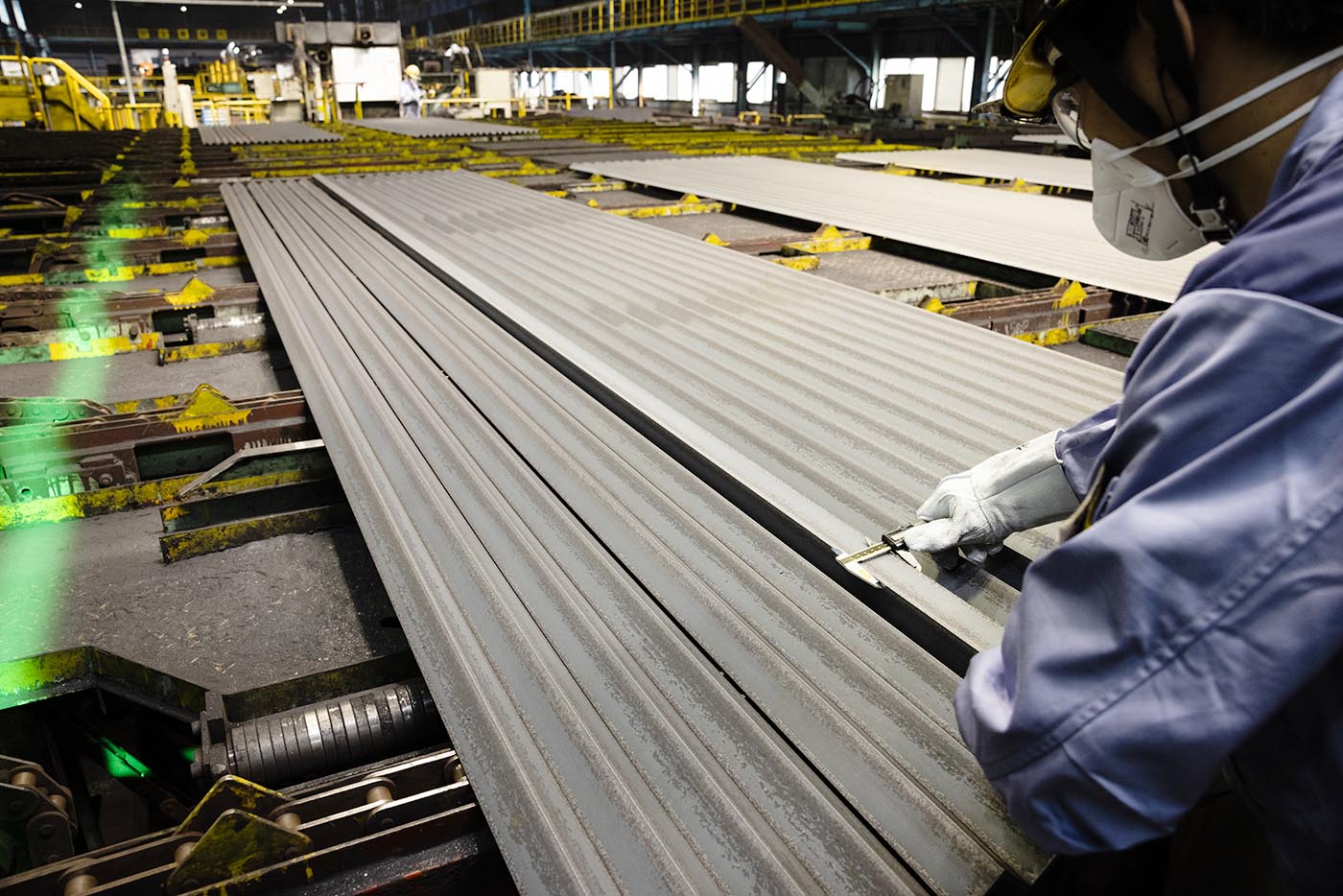
検査
切断後は、製品を検査する。製品の端部には欠陥が出やすいので、傷やつぶれなどを目視でチェックする。また、定期的に寸法が正しいかどうかのチェックも行う。生産工程の紹介はここまでだ。
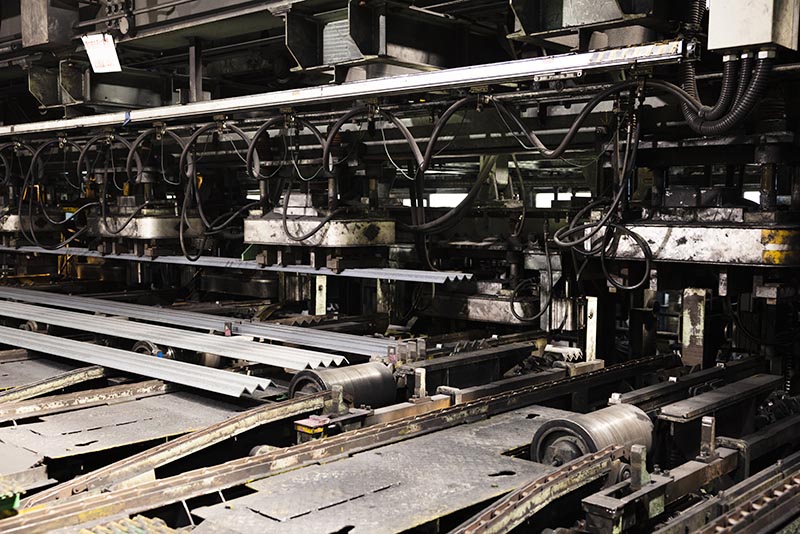
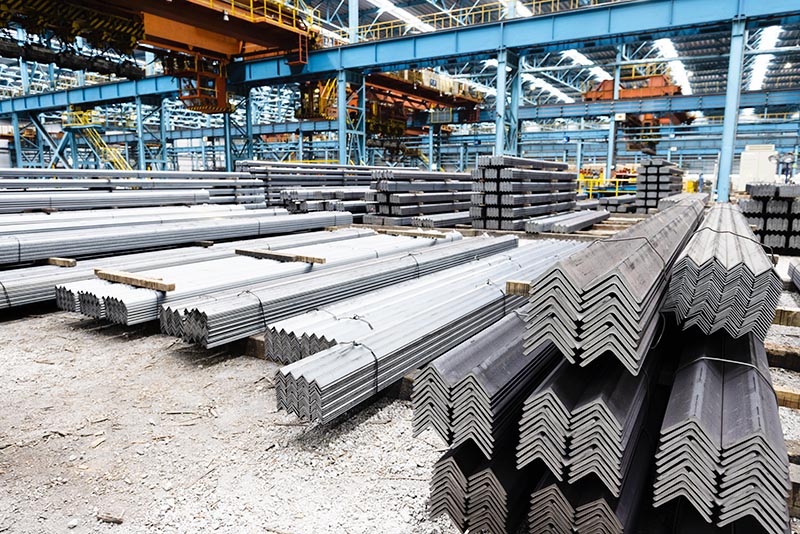
「いい製品を作りたい!」
ここからは、JFE条鋼鹿島製造所での仕事について、圧延工程を管理している木内さんに聞いてみた。
「仕事は、水曜日と木曜日が休みで、昼勤と夜勤の2交代制です。昼勤と夜勤は、一週間ごとに交代します。今日見ていただいた圧延のラインでは、20人が働いています。」
圧延工場は、かなり広かったように思うが、そこで働いている人が20人というのは、驚きだ。なお、この工場で働いている現場の人には、ほとんど異動がなく、圧延に配属されたらずっと圧延なのだそうだ。会社の方針として各分野のエキスパートになってほしいという思いがあるからだ。
実際の製造現場は、どんな感じなんだろう。
「いい製品を作りたい。寸法や幅がきちんと出た、品質の良い製品を作りたいと思っています。でも、崩れるんですよ。製品を作る時には、まずテストを流すんですけど、最初は、だいたいダメです。この状態なら、ここを修正すればいいっていうのがあるんですけど、これがなかなか決まらない。材料の温度や硬さなども違いますし、設備のガイドやロールの位置が微妙に違うこともあって、条件が毎回違うんですよ。それをいかに早く修正するかっていうのが難しい。早く連続した作業まで持って行けた時は、気持ちいいですけどね。」
条件が異なるものの、サイズによって作りにくい部分がわかっているので、過去の生産時のデータを取っておいて、それを活かすこともしているそうだ。
今の課題は、なんだろう?
「今は、燃料費の高騰が課題です。加熱炉が燃料を使うので、製鋼で作ったビレットが冷めないうちにこちらに持ってきて圧延する『直送』を行なっています。それ以外では、新しく作り始めた製品を、早く軌道に乗せたいと思っています。こちらは、ロールの形状が、まだ最適なものになっていないので、今、がんばってやっているところです。」
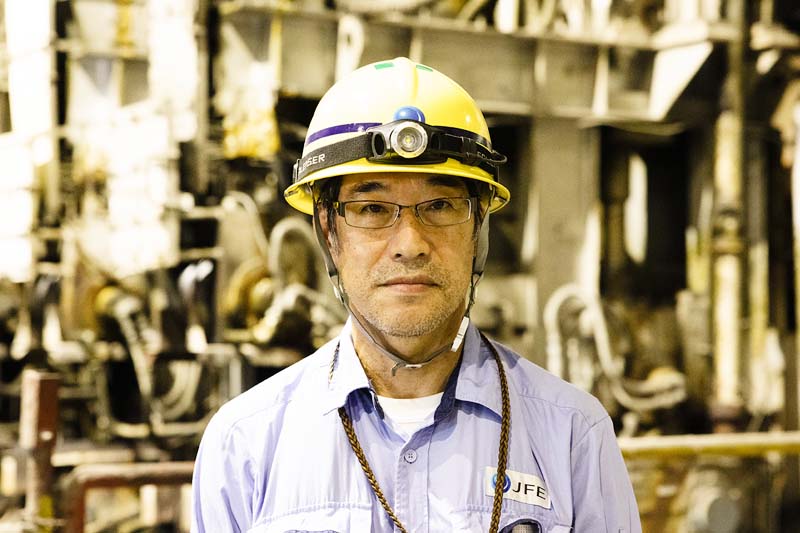
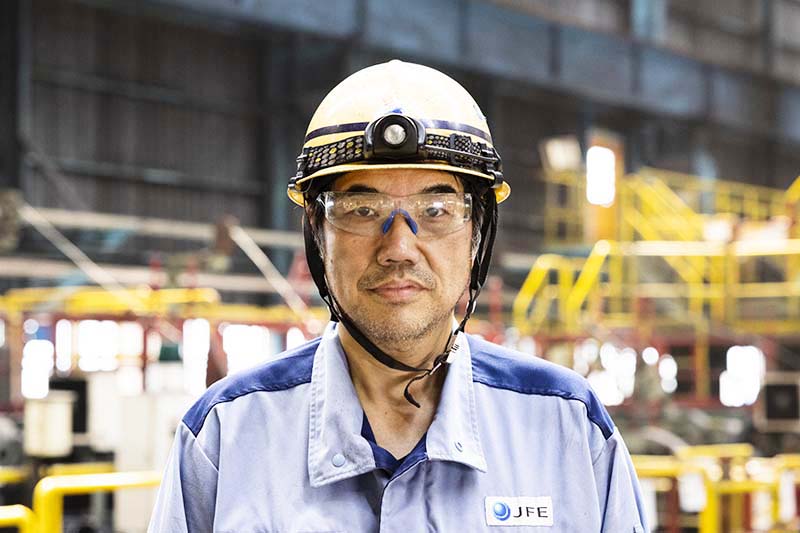
おわりに
この工場では、スクラップから新たな製品を作っているということで、昨今話題の「リサイクル」や「SDGs」といった言葉とも非常に親和性が高い。ただ、運ばれてきたスクラップの山を見ると、正直なところ「これが、製品になるの?」って思ってしまう。材料がいつも違うから難しいという話をされていたが、難しいっていう言葉だけでは表現できない苦労もあるのだろう。また、「燃料費高騰」や「電力逼迫」などについても、個人では、エアコンの使用や遠出を控えようくらいのことしか思いつかないが、工業の現場では、自分が考えているよりも、はるかに切迫した状況になっているようだ。
現場に行って、働いている人たちから直接話を聞くと、ニュースとして流れている情報との温度差みたいなものを感じることが多い。この記事を通して、僕が現場で感じたことの一部でも皆さんに伝わるといいなあと思う。
写真と文 西澤丞 インタビューは、2022年7月に行いました。
2022年10月追記。以下に、同社の水島製造所(岡山県)で撮影させてもらった写真を追加しました。
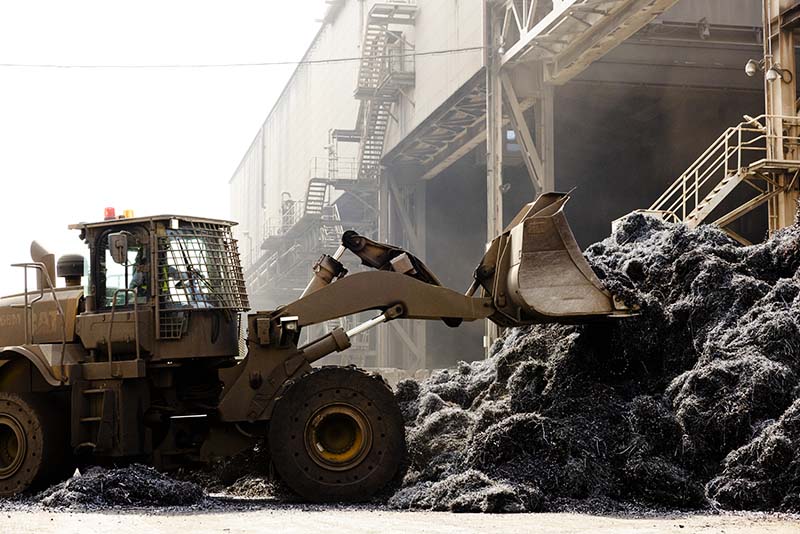
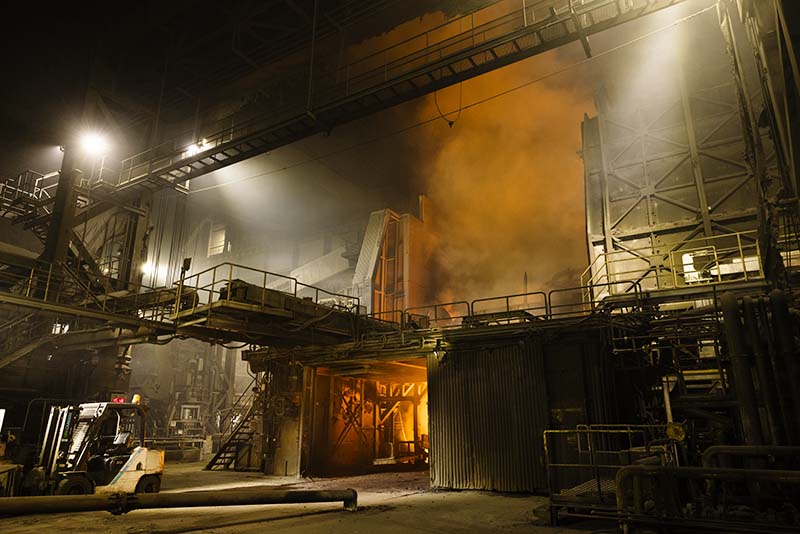
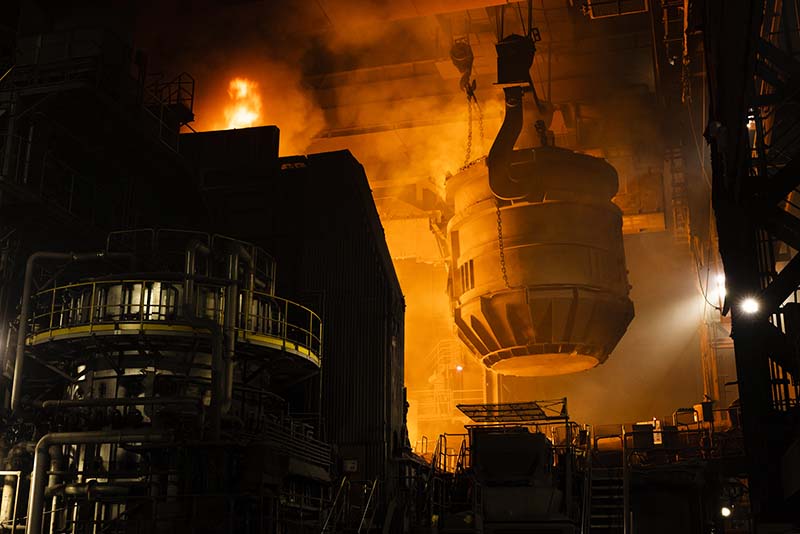
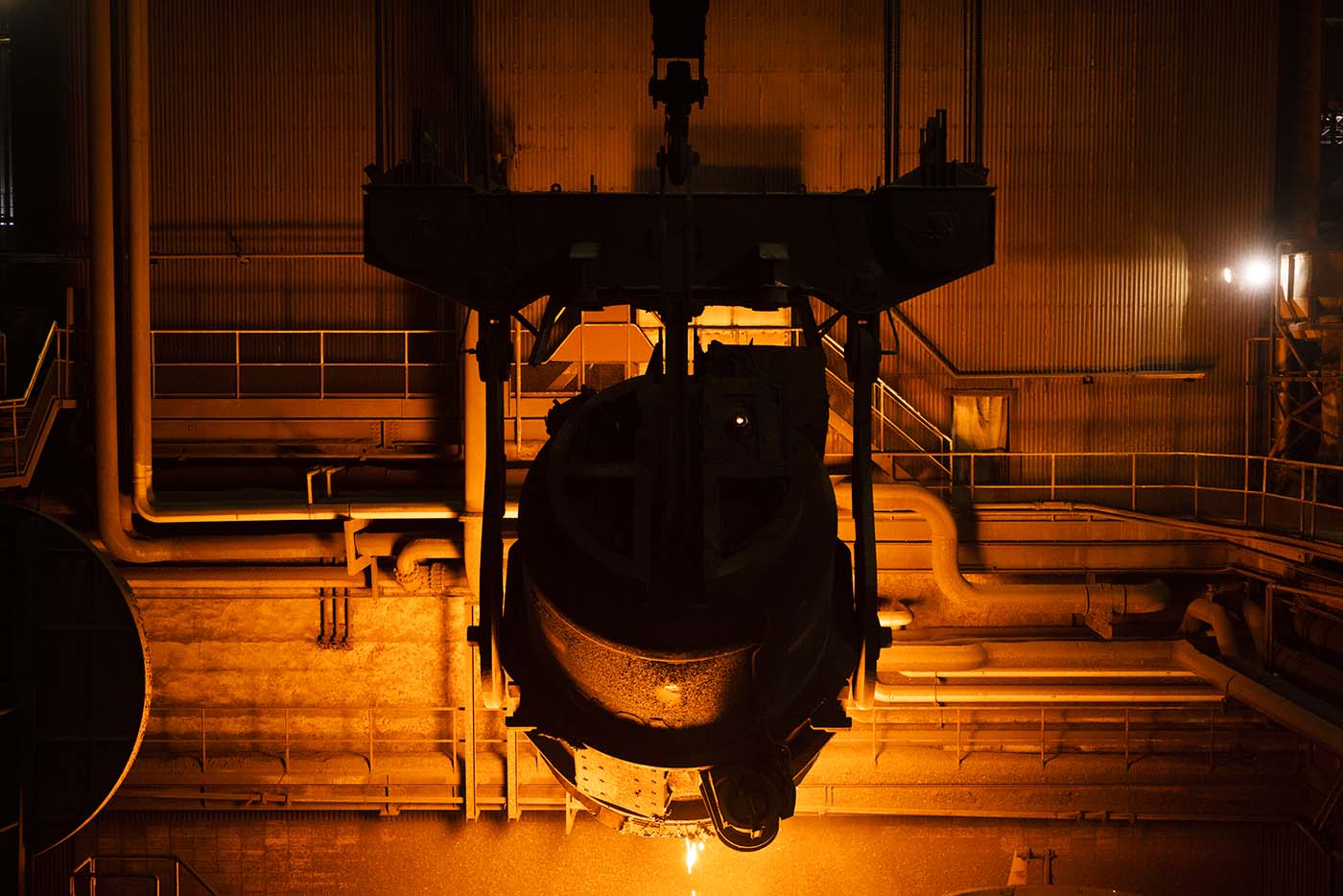

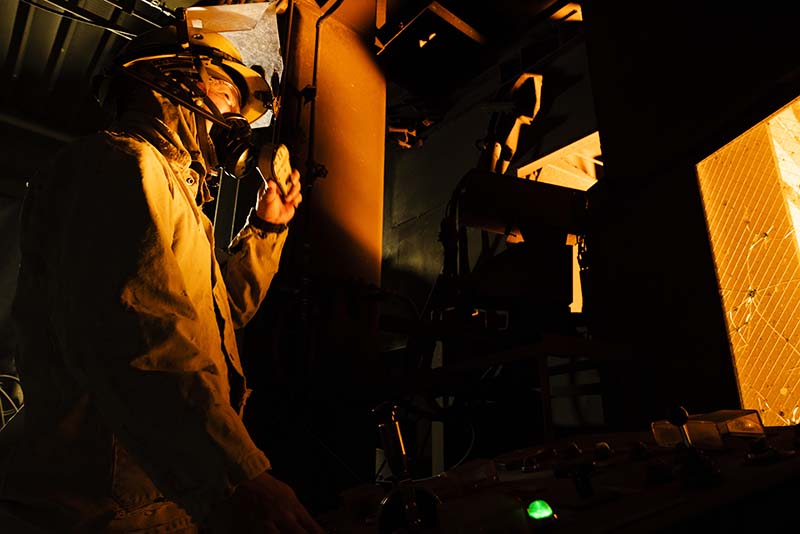
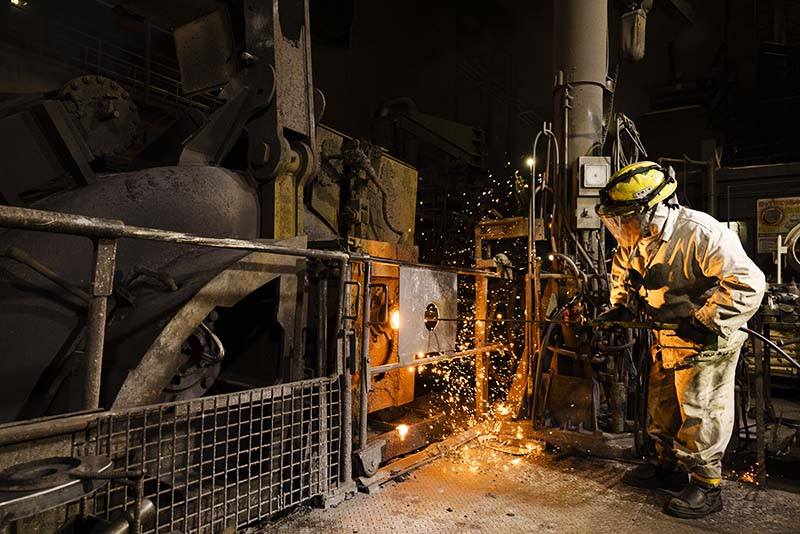
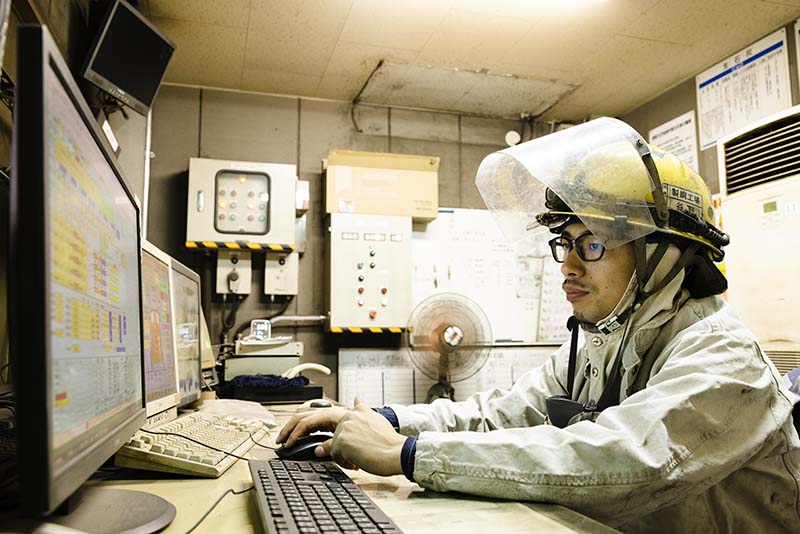
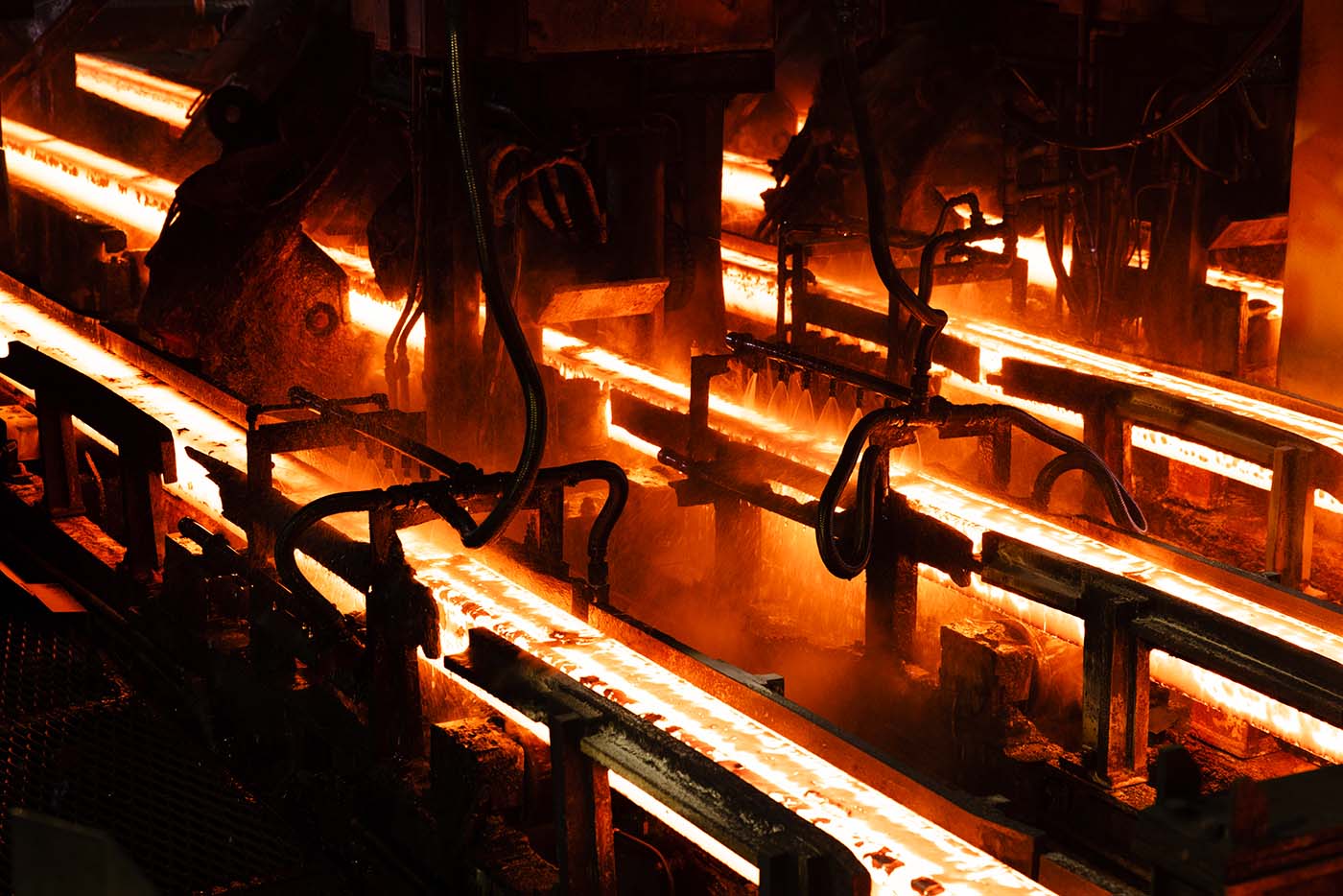

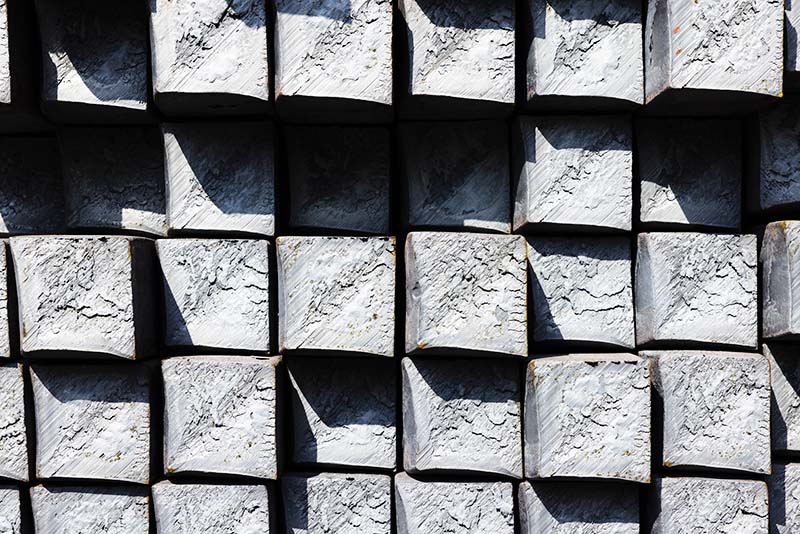
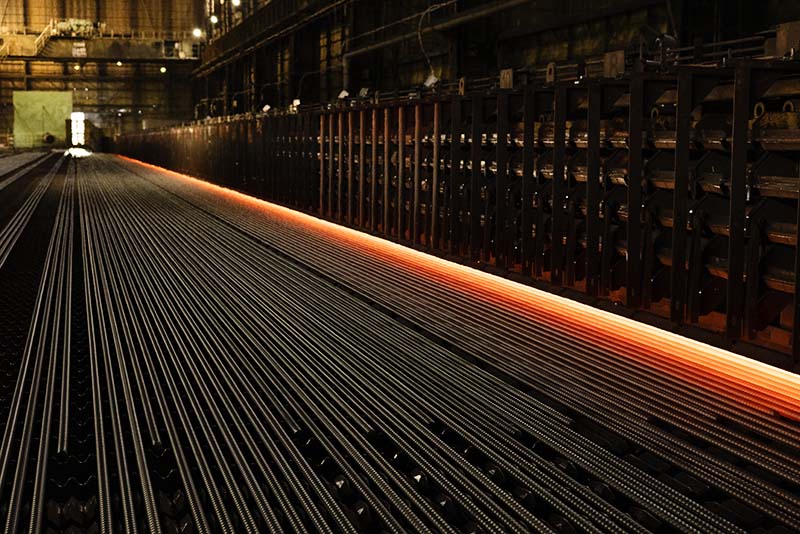
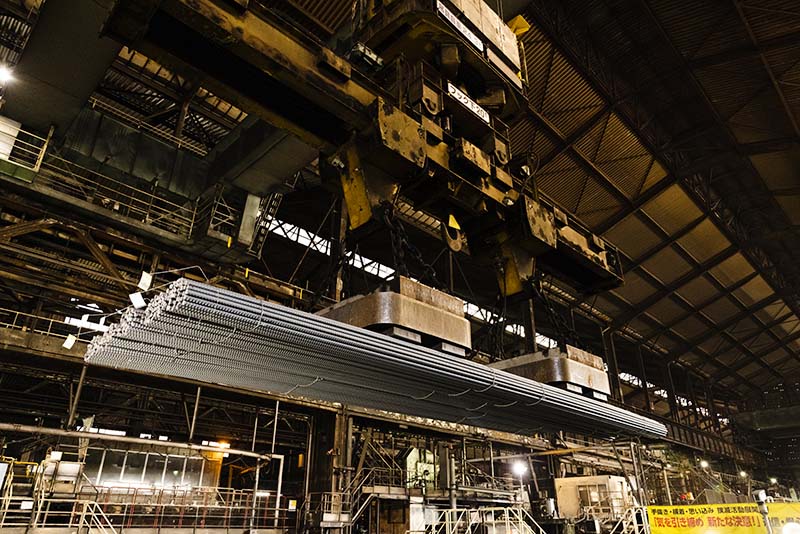